In recent years, many computer-aided methods have been developed to find the most optimum design for a problem. These intelligent techniques have allowed engineers to create designs that were beyond what we could come up with manually. One of these methods is topology optimisation.
Topology optimisation (TO) is a computer-based design method used for creating efficient designs today. Fields such as aerospace, civil engineering, bio-chemical and mechanical engineering use this method proactively to create innovative design solutions that will outperform manual designs.
What Is Topology Optimisation?
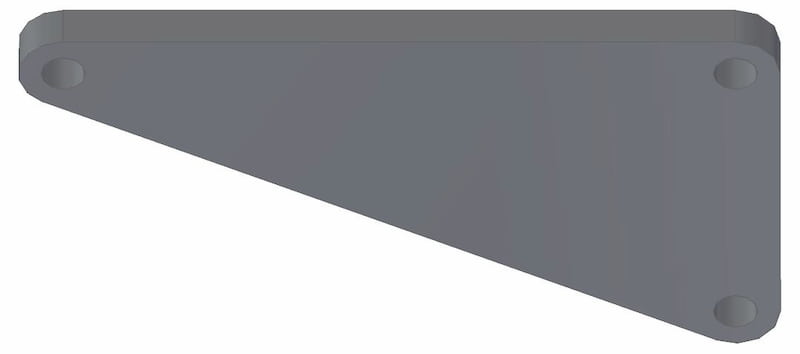
Topology optimisation is a mathematical method used at the concept level of design development. The aim of this method is to spread the amount of material present more effectively over the model. It takes into account the boundaries set by the designer, applied load, and space limitations to create a design.
In simple terms, topology optimisation takes a 3D model and creates a design space. It then removes or displaces material within it to make the design more efficient. While carrying out the material distribution, the objective function does not take aesthetics or the ease of manufacturing into account.Â
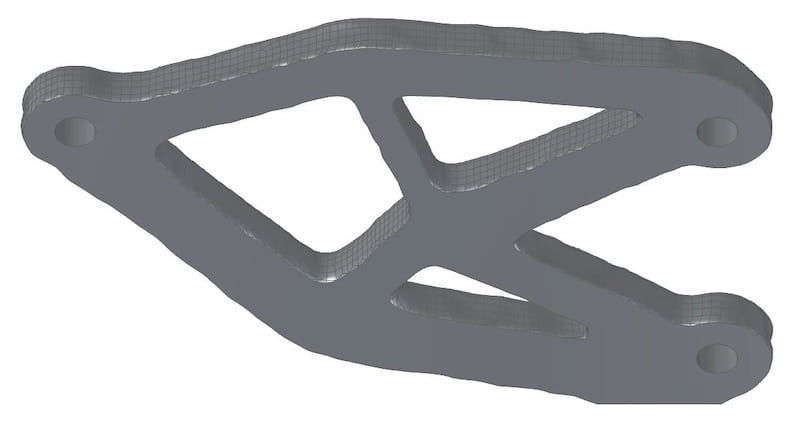
At the very least, the method needs us to provide the magnitude of loading and the constraints within which it should operate. Using this information, the optimisation algorithm creates a possible load path using the minimum amount of material.Â
Once a design is finalised, we use additive (and sometimes subtractive) manufacturing methods to produce the part. As the name suggests, in additive manufacturing (here on out referred to as AM), the material is added (e.g. 3D printing) bit by bit until the final model is complete.Â
AM is capable of creating complex shapes and structures that may be extremely difficult to create using other methods. This is why we prefer it for creating complex products that emerge after optimisation.
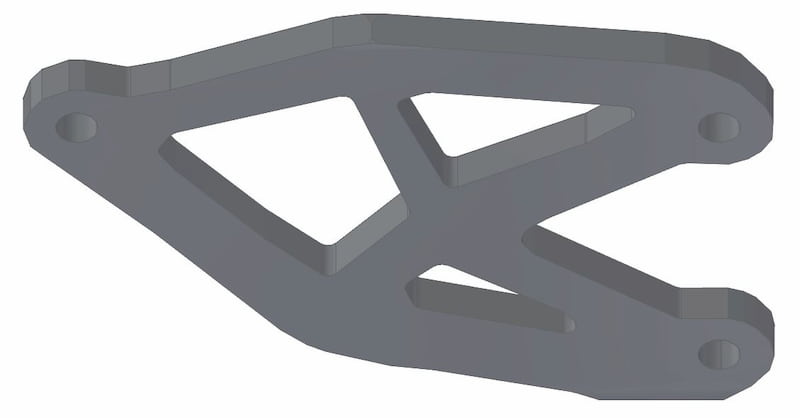
Sometimes, however, the design suggested by topology optimisation is too complex even for AM. In such situations, we make small changes to the design to improve its manufacturability.
How Does It Work?
Topology optimisation is carried out on an already existing model. We can choose to optimise an entire component or elements of it. This area of focus is known as the design space.Â
Topology optimisation uses finite element analysis (FEA) to create a simple mesh of the design space. The mesh is analysed for stress distribution and strain energy. This informs the system about the amount of loading the different sections are handling.
While some sections will have optimal material distribution, there will be some that could use trimming. Sections with low strain energy and stress level are marked using the finite element method. Once all the inefficient sections within the design space are identified, the objective function gradually removes the material.
During this trimming process, the system will also check how much the overall structure is affected by the removal process. If the removal process compromises its integrity, the process stops and the material in that region is retained.
Before running the TO algorithm, we set the amount of material we intend to remove as a percentage of the total material. For example, we may set the target material reduction percentage at 50%.
The system removes the excess material in stages. At every stage, it checks the structure for stress levels by reiterating the element distribution until it reaches the target percentage.
- Personal account manager
- Quality assurance
- Payment terms for companies
- On-time delivery by Fractory
Benefits
Topology optimisation improves upon several challenges at a time. Let’s see what advantages TO has to offer.
Create cost and weight-effective solutions
The most attractive benefit of topology optimisation is its ability to reduce any unnecessary weight. Size optimisation means that less raw material is needed.
Extra weight also negatively impacts energy efficiency. Parts will cost more for shipping as well. All these advantages translate directly into actual cost savings which is important in a competitive market.
A great example is how General Electric used TO to reduce the weight of an engine bracket by 84%. This modification in a small part saved the airlines nearly $31 million dollars by improving the overall energy efficiency.
A faster design process
As design constraints and performance expectations are factored in at the early stages of conception, it does not take as much time as without TO to come up with the final design.
A faster process also means a shorter time-to-market duration which is especially important for new products in a competitive market.Â
Sustainability
Topology optimisation prevents undue material wastage. The algorithm is capable of creating sustainable building systems while still being rooted in sound structural logic. Also, as mentioned earlier, topologically optimised products save fuel through weight reduction.
As the demand for sustainable alternatives increases, more and more industries in the manufacturing sector are employing TO due to its environmentally friendly nature.
Disadvantages
There are some topology optimisation problems that we must know about in order to use it effectively. Let us see what they are.
Production limitations
The designs that TO comes up with can be difficult to manufacture. Given that AM is quite flexible in terms of what it can manufacture, it is still necessary to check for manufacturability prior to finalising the design.Â
If we try to solve the topology optimisation problem thinking only about the function, it is possible that we may fall short when it comes to our build quality and efficiency.
It is worth noting here that a few software vendors offer a feature called manufacturing constraints for TO. Thus, it is possible to create parts that are only manufacturable using conventional methods.
High cost
Lately, the cost of AM has reduced but it is still a notch above traditional production methods. We need to consider the cost to benefit ratio on a case by case basis.Â
For mass production, creating injection moulds is a possibility. Therefore, we can look further than 3D printing for creating plastic parts.
For making a few components on and off, AM could prove expensive which is a deterrent in most cases as the investment is too high. In such cases, it will be more beneficial to outsource the production to a 3D printing service company.
Applications of Topology Optimisation
Many industries are now looking towards advanced design methods like topology optimisation and generative design. Although the production of parts may be costlier, there are important advantages on offer.
Aerospace, medical and automotive industries are some of the ones looking for assist from these mathematical modelling methods.
Aerospace
Air travel is costly. Since the very beginning, attempts have been made to reduce the mass of an aircraft as far as possible without compromising its strength.
Topology optimisation helps analyse aircraft components in detail to chop off unnecessary component mass. This means an aircraft can carry more cargo (or use less fuel) on the same journey.
The same benefits apply to satellites and rockets. This mathematical method helps reduce support structures and create lighter parts while retaining their original strength.
Medical
In the medical field, topology optimisation creates highly efficient implants and prosthetics. Using the algorithm, we can create parts that imitate the bone density and stiffness of the patient. It further takes into account the patient’s anatomy and the designed part’s activity level and the load applied.Â
The optimisation improves the part’s endurance limit. Where feasible, the algorithm will replace the solid structure with a lattice. This reduction in weight is a welcomed benefit for implants/prosthetics.
Automotive
Some automobile makers are now using topology optimisation for designing structural (chassis) as well as machinery components. This technology has helped in reducing the mass of the body skeleton while maintaining (and even improving in some cases) the overall strength of the initial product.
Now, in addition to composites and adhesives, steel is finding more applications due to the possibility of creating complex lattice structures using AM.
Manufacturing Methods
Topology shape optimisation can create complex structures that have the best stiffness-to-weight ratio while using minimum material. They may be manufactured using additive as well as subtractive manufacturing processes.
AM does give a large amount of freedom to the designer but where flat products are concerned, advanced subtractive manufacturing methods can create parts with complex geometry just as effectively.
Each method will impose different manufacturing constraints on the topology and geometry of elements and how the production process will go about with its creation. Some excellent methods that can manufacture these innovative solutions are:
3D printing
3D printing has been instrumental in bringing topology optimisation to the limelight. Without additive processes, it is nearly impossible to create complex structures designed by many other optimisation techniques, especially generative design, in addition to TO.
3D printing offers a fast and efficient way to create topologically optimised products with little to no wastage. There are many advantages to 3D printing and very few limitations. Among the limits of 3D printing is that only a handful of metals can be used with it as it was originally designed for plastics.
CNC machining
As the use of topology optimisation became widespread, efforts were made to add features to computer programs that allow traditional production methods to create these components.Â
As TO creates hollow structures with support structures of non-uniform thickness, it is difficult to use CNC machining for intricate components. But for models where the visual capacity overlaps with Vmap (Visibility map) completely, the part is manufacturable with CNC.Â
Visibility is a concept defined in production to understand the capacity of a particular process to create a certain part. In practical processes, a part is said to be visible if no points on its surface are hidden from the process directions. Needless to say, a 5-axis CNC machine will be able to manufacture products of greater difficulty than a 3-axis CNC machine.
Laser cutting
Laser machining can also work as a production process for topology optimised products. This method is capable of cutting intricate shapes with enviable accuracy.
Laser cutting can be used on several different materials (metals, wood, acrylic, MDF) making it more useful when subtractive manufacturing is possible for a TO part.
Topology Optimisation Software
There are over 30 software products available in the market for topology optimisation which come with their own tradeoffs. Some programs are more popular than others for their holistic approach to the technique. Let’s take a look at some of them.
Ansys Mechanical
Ansys creates design solutions for multiphysics engineering simulation. The Ansys Mechanical software comes preloaded with structural topology optimization features. This program can analyse and optimise simple as well as complex design spaces and make corrections where needed.
It comes with features such as:
- Modal analysis of multiple static loads.Â
- Control options for setting minimum material thickness.Â
- Ability to work with planar and cyclic symmetry.Â
- Easy validation of results.
Altair Inspire
Altair’s Inspire is a powerful tool when it comes to topology optimisation. It also features added capabilities such as generative design and rapid prototyping.
The program is easy to master and provides important features such as:
- Capable of generating mixed support structures having solid as well as lattice geometry. These files can be observed in 3D and can be sent directly to a 3D printer for production.Â
- Ability to interact and assign new loads to the structure besides being capable of running predetermined loads that can be imported/exported for analysis.
- Ability to reduce overhangs to encourage more self-supported structures.Â
Solidworks
Solidworks added topology optimisation features in its 2018 update. This is a widely used computer program for CAD applications and the introduction of TO has been quite smooth and efficient.
Solidworks also uses the subtractive method where it chisels away material to reduce mass and improve stress distribution.
The distinct features of the Solidworks TO module are as follows:
- Ability to bring optimized designs into a CAD environment using multiple methods.
- The availability of various partner products.
Conclusion
Advances in AM have enabled us to create extremely complex shapes with relative ease. To take full advantage of these leaps in production capabilities, we need technologies like topology optimisation.
TO is great at optimising designed solutions. Sometimes, it can feel a bit out of control especially if you are still learning the ropes. However, there are many factors that can be controlled to shift the model toward a more favourable outcome.
Some of these controls include restricting member size in design space, demanding symmetry about planes, or extrudability of the final model. You can also manipulate the material removal percentage to control the alacrity the algorithm will optimise the part with.