304 and 316 stainless steels are ferrous metals that are widely used when corrosion resistance is sought. Even though called stainless, they are not. It just takes more time and harsher conditions to see the first signs of wear.
They still make for a great solution in difficult environments, providing long-lasting products in many fields. Let’s delve deeper into the realm of stainless steels and try to find the difference between 304 and 316 grade stainless steels.
Common Applications for AISI 304 & 316
Stainless steels are known for their resistance to corrosion. The combination with strength and low maintenance make them a great fit for a wide range of applications.
They are used everywhere from buildings and constructions to medical and food equipment. In some cases, avoiding rust can be a matter of a construction’s longevity. Corrosion can eat away at metal and your construction’s load-bearing capabilities will diminish over time.
Temperature changes can have a large impact on corrosion. It accelerates the process, thus making the conditions harsher. Stainless steels are suitable for such an environment. Much more so than coated structural steels, as the coating is more easily damaged in this kind of a situation.
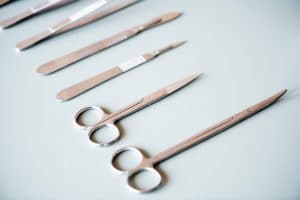
Stainless steels are a perfect fit for hygienic environments. Those include the aforementioned medical and food equipment examples. On one hand, they don’t react with corrosive acids (like orange juice). At the same time, surgical instruments and cutlery made from stainless steel are easy to clean and disinfect.
The last reason for using stainless steels is aesthetics. You don’t need to powder-coat them to fight corrosion. Therefore, a beautiful metallic look is possible without specks of rust hurting your eye.
You can also choose from a large variety of stainless steel finishes. These provide you with options for any application.
Layer of Oxidised Chromium
In case of structural steels, you have to add a layer of protection by coating it. Otherwise nature will do its own thing and iron starts to corrode by forming iron oxide. The flakes of rust begin to crumble, exposing more metal to the outside conditions. All this ends in piles of scrap metal.
In case of stainless steel, a protective layer forms itself. Chemical reactions still take place, but they don’t include iron. Chromium, which is present in every stainless steel (at least 11%), is the one that oxidises.
The oxidised chromium forms a protective layer that has a thickness of only a few molecules. Although seemingly nonexistent, it is highly durable and non-reactive. If the layer gets damaged, it will repair itself. The quickness of this process depends on the amount of chromium in the steel.
Mechanical Properties of AISI 304 & AISI 316
Stainless steels are divided into 5 families: austenitic, ferritic, martensitic, duplex (a mix of ferritic and austenitic) and PH – precipitation hardening (martensitic, semi-austenitic or austenitic). AISI 304 and AISI 316 have an austenitic microstructure, like 90% of the stainless steels consumed, thanks to nickel content. What does it actually mean to you?
Let’s skip the structural differences for simplicity’s sake and move straight to how this structure affects the mechanical properties of materials. The features of austenitic stainless steels are:
- Excellent corrosion resistance in normal or mildly aggressive environments
- Great performance at low temperatures
- Good performance at high temperatures
- Easily work-hardened
- Good ductility and formability
- Excellent weldability
- Great suitability for hygienic environments
- Non-magnetic
Tensile strength, Rm, MPa | 0,2% Yield strength, Rp0, MPa | Brinell hardness, HB max | |
---|---|---|---|
AISI 304 |
540 – 750 | 230 | 130 – 180 |
AISI 316 |
530 – 680 | 240 | 120 – 180 |
The stainless steel mechanical properties table shows that while the yield strength of AISI 304 and AISI 316 may be comparable to structural steels, they outperform the regular steels in tensile strength. Still, neither of those options is best suited when something reliable against abrasives and hard wear is sought. The ideal solution then is wear-resistant steels, like Hardox.
- Personal account manager
- Quality assurance
- Payment terms for companies
- On-time delivery by Fractory
Grade Meaning
AISI stands for American Iron and Steel Institute. Therefore, both grade 304 stainless steel and grade 316 conform to the American standard. The European equivalents are 1.4301 and 1.4401, respectively. You can probably see why people usually choose to go with American standards here.
But what do the grades of stainless steel mean? Basically, they indicate the steel’s structure. Grades 3xx mean that the structures are austenitic.
Some of the alloys have a suffix L added to them. When comparing AISI 316 and AISI 316L, we can see pretty much identical chemical compositions. Still, there is a minor difference – L stands for “low” as in low carbon content.
This results in a minor difference in strength, which is in favour of AISI 316. Why use AISI 316L then? The welded joints there do not respond to corrosive environments as easily. The need for annealing the joints is eliminated. Also, 316L is very well suited for high-corrosion environments like marine equipment.
The same principles apply to AISI 304 and AISI 304L. AISI 304 steels are lower priced but also less resistant to corrosion.
Chemical Composition
Component |
Content % by weight | |
---|---|---|
AISI 304 |
AISI 316 |
|
Chromium (Cr) | 17,5 – 19,5 | 16,5 – 18,5 |
Nickel (Ni) | 8 – 10,5 | 10 – 13 |
Molybdenum (Mo) | Trace amounts | 2-3 |
Manganese (Mn) max | 2 | 2 |
Silicon (Si) max | 1 | 1 |
Nitrogen (N) max | 0,11 | 0,11 |
Carbon (C) max | 0,07 | 0,07 |
Phosphorus(P) max | 0,045 | 0,045 |
Sulfur (S) max | 0,015 | 0,015 |
Iron (Fe) max | Makes up the rest | Makes up the rest |
At first glance, the chemical compositions of AISI 304 and AISI 316 don’t differ much. A few percentages this way or that in chromium and nickel. The difference derives from molybdenum. While grade 304 stainless steel only has trace amounts of it, AISI 316 has considerably more.
Addition of molybdenum increases corrosion resistance of 316 stainless steel, especially against pitting and crevice corrosion in chloride environments.
AISI 304 vs AISI 316 – Which to Choose?
As you can expect, there is no single answer. Otherwise we wouldn’t even need the different grades. Each has their own uses and you have to select one according to your needs. We can just look at some questions along with answers to aid you.
What is the corrosive environment? If it’s salty or acidic, go with AISI 316. This is the main and clearest dividing line of the two stainless steels. As said, molybdenum makes the difference.
What is the temperature of operation? High temperatures accelerate corrosion. Thus, a higher grade is better suited.
What is your budget? If the conditions don’t warrant the need for AISI 316, it is cheaper to go with AISI 304. The former costs about 25% more than the latter.
Hopefully we managed to make your material selection process a bit easier. You can now go and compare the prices of AISI 304 and AISI 316 by using our stainless steel laser cutting services.