Design to Cost is a part of Design for Excellence (DFX) philosophy along with its other branches such as Design for Manufacturing (DFM), Design for Assembly (DFA), Design for Supply Chain (DFSC) and Design for Sustainability (DFS) to name a few.
As over 70% of the product’s final cost is determined during the design stage, Design to Cost methodology is an important approach for manufacturing companies to achieve a more precise cost estimation.
What Is Design to Cost?
Traditional approaches have considered product cost an important factor in later development stages and independent from design decisions. This can result in estimated product costs that are significantly higher than target costs. In some cases, even redesign might be needed which would become an additional investment.
Design to Cost or Design for Cost or DTC is a cost management principle that accounts for development, production and service costs at the design stage. Design to Cost also aims to implement the necessary cost strategy during the development cycle of the project so that cost targets will become independent variables to guide the decision-making.
Design to Cost shouldn’t be seen as the same as target costing. While target costing takes a broader approach—encompassing administrative, marketing and other activities—DTC focuses exclusively on managing costs during the design phase. In target costing, a specific cost target is set from the start, whereas DTC integrates cost management as a guiding factor throughout the design process to ensure that cost targets are met without requiring later adjustments or redesigns.
Design to Cost Phases
To implement effective DTC before the production process, a strategic foundation should be followed.
Defining Target Cost
The first stage in applying design to cost is to define the acceptable cost of the final product. This can be done by creating multiple standards or tiers for the outcome. The basic standard or lower tier would have only the essential quality and functionality. A tier above this would have some innovation and extra features. The top tier would add even more functionality and luxury. The latter can also be considered as design to value, a concept explored in cost and value engineering, which looks at optimising cost efficiency while maintaining high product value and functionality.
Depending on the project type, any one of these tiers can be used as a starting point at this stage. This is an essential part of DTC as it will help to understand the needs and scopes of the client and lay out the framework for the following stages.
Cost Management and Cost Reduction Strategies
This stage is at the core of Design to Cost methodology. The following section will lay out different cost drivers to bear in mind in the product design phase that will influence the final product’s price.
Design standardisation
One of the most important aspects of design development in any manufacturing industry is the standardisation of design across the product range. This should take into account any materials used while aiming for modular design as this helps to reduce fixed costs greatly. This strategy is definitely not exclusive to Design to Cost methodology as it is also one of the key focus points for Design for Assembly & Design for Manufacturing & Assembly.
Use of standard parts
The use of standard parts is another great way to further reduce production costs. Collaboration with the suppliers of these parts can also increase flexibility. When standardisation is implemented across the entire supply chain, it reduces the set-up and inventory cost, thereby simplifying supply chain management. Thus this strategy is also in the focus of Design for Supply Chain. And finally, there is the added benefit of reducing costs associated with R&D.
Geographical factors
Manufacturing location is a crucial aspect of cost management. There are multiple important geographical factors to consider while making this decision such as supply chains and ecosystems, the availability of components, matters related to labor, taxes and duties.
Packaging & transportation
Weight and volume are the keywords when considering transportation and together with packaging, these should be accounted for in the design process.
Waste minimisation
One of the most important concepts in terms of waste minimisation is lean manufacturing. The focus here is on reducing waste in all production stages. Any feature on the final product that doesn’t add value to the client is also seen as waste and should be thus removed from the product at this stage.
Maintenance
While not a part of the production process, maintenance should not be forgotten as a cost within the design. The right design decisions can increase maintenance intervals and accessibility for difficult areas. Having a maintenance-friendly design in focus can thus reduce future costs after the production cycle.
None of these factors can be viewed in isolation as they’re all intertwined and have direct costs. Design to Cost should always be seen as a wide-ranging approach that can include a multitude of concepts. Depending on the project type and requirements, the design team should decide which aspects are most appropriate when considering DTC.
Analysing Results
This is the most important stage in DTC as it will determine manufacturing decisions. When analysing results it is important to evaluate if the design at hand fits the objectives or if it can be improved. The design to cost process should be repeated until the design fits the objectives, surpasses them or cannot be improved further.
- Personal account manager
- Quality assurance
- Payment terms for companies
- On-time delivery by Fractory
Challenges in Design to Cost Implementation
The development of design to strategy can pose multiple challenges. The following sections address some of the most prevalent ones.
Job responsibilities
One of the most prevalent challenges around product cost is the uncertainty in terms of responsibility. To overcome this, design engineers should be allowed both the freedom and responsibility along with the necessary tools to implement cost management via design solutions.
Engineering culture
Another difficult aspect when putting design to cost into practice is the engineering culture as product engineers may not have an overview of many of the important cost drivers. For addressing this issue, engineers need resources to understand costs at the design stage. This should be achieved without the unnecessary burden of expert resources.
Component-level knowledge
To implement all of the aforementioned cost management strategies, the design engineering team needs to have a component-level knowledge of the manufactured product.
How to Compare Costs
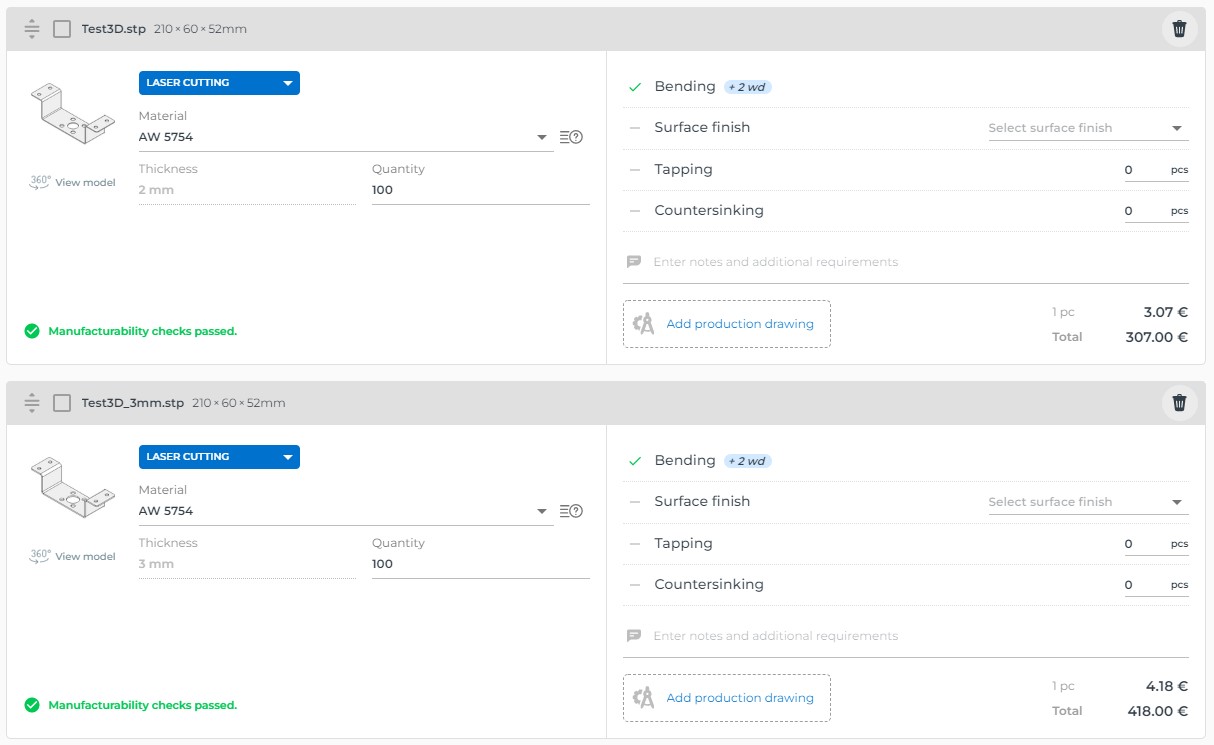
It’s actually quite easy to do by utilising the capabilities of our free-to-use manufacturing platform. The combination of manufacturability checks and instant pricing on makes for a great tool for evaluating costs in the design process. You can optimise the part geometry, use of materials, etc. for cost-efficiency based on platform feedback. All of those decisions require a case-by-case evaluation and require the designer to be in the loop with all of the end product requirements but the platform can offer great Design to Cost feedback.
In the picture above, you can see that both of the brackets are made from the same aluminium grade sheets but the difference lies in the thickness. In a lot of cases, products are over-dimensioned and made to endure loads and environments to which they will never be exposed. Using thinner sheet stock can be a great way to cut down on costs but again, the design engineer has to be up to date on all of the functional requirements to do so. These little cost savings really do add up, especially when moving on to high-volume production.
Below, we’re comparing a stainless steel bracket to an aluminium one. The brackets are exposed to the elements in their working environment but they don’t serve a structural role in the assembly. The AW 5754 H22 marine grade aluminium offers excellent corrosion protection but so does making the part from AISI 316 2B stainless steel. AISI 316 2B has better protection against acidic and salty environments than the more common AISI 304. As you can see, the price per piece is cheaper for the parts made out of aluminium and since they do not bear great loads and endure extreme forces, producing the brackets out of aluminium makes more sense.
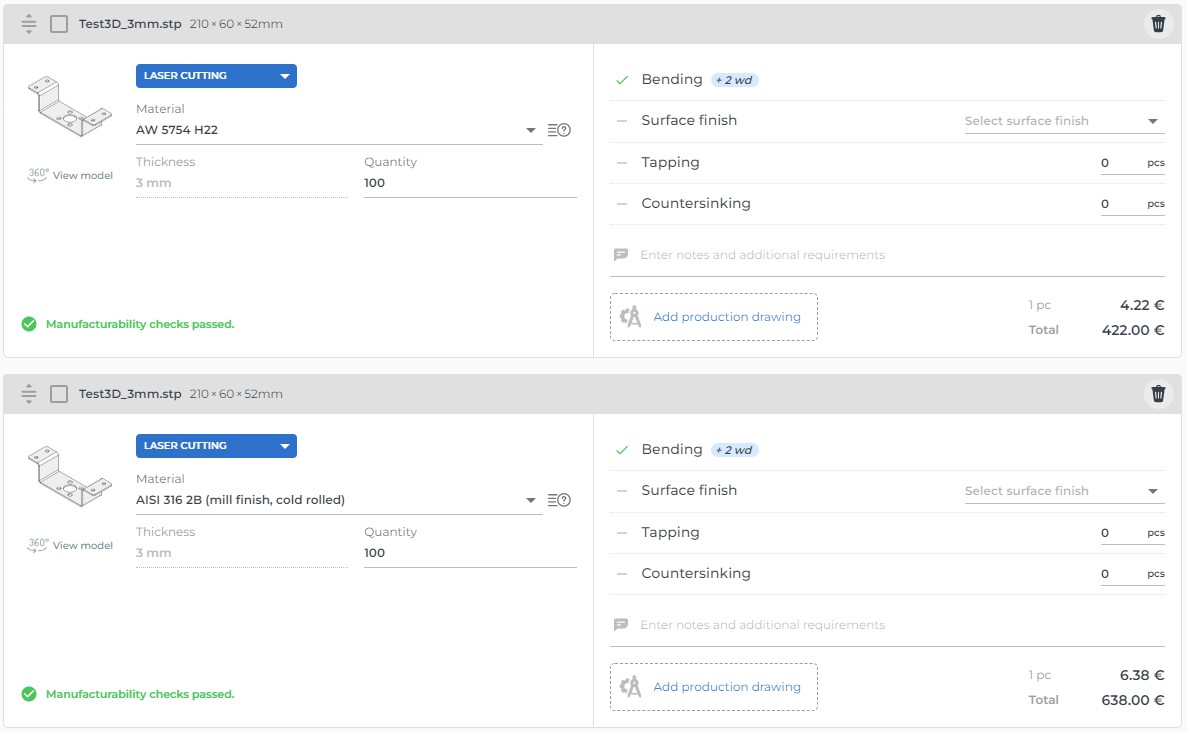
In addition to the cost information, our platform gives feedback on the manufacturability of parts based on your 3D models, so you can fix any issues to speed up the time to production.
Conclusion
As a part of Design for Excellence, Design to Cost is a great methodology to provide cost models via design decisions. The key benefits of implementing this strategy come from cost reduction and savings at the beginning of the design. As an additional benefit, cost estimations can be achieved with relatively limited information.
It is important to bear in mind that DTC is not a definitive ruleset but a framework that should be adjusted according to requirements and possibilities and the variability between different projects.
Design to Cost can pose multiple challenges during implementation, but these can be overcome with smart and efficient management while making available all the necessary tools and resources for the design team to have an in-depth understanding of its concepts.
As DTC is becoming more prevalent, we can expect future research done in this area which can provide manufacturers with further information to optimise costs and increase system performance.