There is a wide variety of Lean Manufacturing methods. Each of them has specific requirements and benefits. All of the lean tools have different approaches to problem-solving.
This article describes some of the most common Lean Manufacturing techniques and tools. But first, let’s make sure we understand what Lean Manufacturing is.
What is Lean Manufacturing?
Lean Manufacturing or Lean Production is a series of methods that are based on the Toyota Production System created by Taiichi Ohno. First implemented in the 1940s and developed until the 1970s together with Eiji Toyoda. The term “lean” was taken from John Krafcik’s 1988 article “Triumph of the Lean Production System.”
The main objectives of lean manufacturing are:
- Minimise waste and costs.
- Maximise productivity and quality.
- Ensure continuous improvement.
These objectives are achieved by following the principles described by the Toyota Production System. They have now become synonymous with Lean Manufacturing principles and are applied all over the world by project management.
Lean Manufacturing Principles
These are the principles to follow when applying Lean Manufacturing:
- Maximise share of value-adding activities.
- Implement stable and standardised processes.
- Create a self-learning, continuously improving organisation.
- Take a holistic supply chain perspective.
- People development is the key success factor.
How to Apply Lean Manufacturing?
The first step is identifying what is known as the seven wastes of lean. The objective of Lean Manufacturing is to eliminate waste. These wastes are described by the Toyota Productive System as follows:
Transportation
This waste involves the unnecessary movement of materials or people within a process. It can result in production delays, handling damage and extra time that doesn’t contribute to productivity. Long transportation also impacts communication which affects the quality of the product.
Examples of transportation waste include:
- Temporary storage of work-in-progress (WIP) instead of moving the WIP to the next step
- Frequent transport of raw materials or parts within the factory due to poor layout
Inventory
This refers to the storage of raw materials, work in progress or finished goods. It usually means there are problems in the process that are hidden behind rising stock levels. This results in increased operational costs and production lead times.
To address these challenges and optimise warehouse space, businesses can explore the benefits of warehouse mezzanine systems offering an efficient solution to maximising vertical space utilisation within a warehouse facility.
Motion
Although seemingly similar to transportation, it is not the same. The motion refers to the unnecessary movement of people or machines within a process.
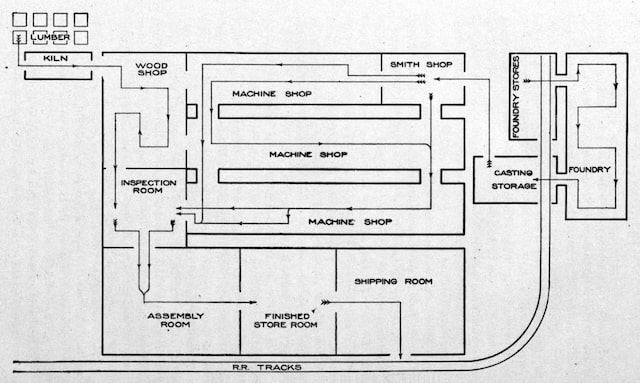
Some examples of motion waste include:
- Movement of people to fetch tools for a changeover process
- Movement of machine operators between different controls of a machine
- The necessity to stretch or bend over to complete a task
Waiting
This waste involves people or machines waiting for the completion of a work cycle. For example, waiting for raw materials to arrive, waiting for a process to finish or waiting for maintenance.
Over-Processing
Over-processing refers to waste related to an operation or process that is not necessary to meet customer demands. Examples of over-processing are:
- Producing to specifications tighter than the customer requires
- Unnecessary quality checks
- Performing operations that are not required to produce the final product, etc.
Overproduction
It means producing sooner, faster, or in greater quantities than customer demand. Over-produced items end up as inventory or scrap, thus creating more waste. Moreover, overproduction takes time away from value-added activities.
Some examples of overproduction are:
- Producing in larger batches to avoid changeovers
- Producing more than requested because of potential quality issues.
Defects
It refers to producing products that do not meet specifications. Examples of defect waste are:
- Re-working products because customer specifications are not met
- Delays due to re-adjusting equipment or processes until the product parameter reaches the target
- Scrapping defective products, etc.
These are the seven wastes of lean as described by the Toyota Productive System. However, some experts in the Lean Manufacturing field say there is an important eighth waste that must be considered. They describe it as human waste which refers to talent and skills being misused.
After these wastes are identified, it is time to put one or more Lean Manufacturing techniques into practice. Here are some of the most used Lean tools.
13 Lean Manufacturing Techniques
Bottleneck Analysis
There is an important practice in Lean Manufacturing, which is measuring processing times and flow times for each productive process. These times make it possible to calculate the process capacity in order to identify the bottleneck activity.
A bottleneck activity is something that limits the turnout of the process. After identifying the bottleneck, actions are taken to improve the performance of the activity, thus improving overall productivity.
Takt Time
Takt means “cycle” in German. This Lean Manufacturing technique helps to determine the cycle of production.
This time is calculated by dividing the time available in a period by the demand in a period. For example, 480 minutes of work per day (8h) to produce 2400 units results in a takt time of 480/2400 = 0.2 minutes.
By calculating this time, it is possible to align the pace of production with customer or market demand. As such demands are subject to change, takt time analysis can be considered a form of lean continuous improvement. Processes can be continuously optimised in response to live changes in demand. This usually results in a reduction of transportation, inventory, motion, waiting, over-processing, overproduction and defects. So all the seven wastes of Lean Manufacturing.
- Personal account manager
- Quality assurance
- Payment terms for companies
- On-time delivery by Fractory
Batching
Batching, also known as cellular manufacturing, is another popular Lean Manufacturing technique. This lean tool looks at the optimal use of machinery to achieve a continuous flow in serial production.
For example, let’s say you are manufacturing 2 separate laser-cut parts for a series of machines on the same workbench. Batching means that those 2 parts should be produced in batches. Thus, you don’t need to set up the machine for each part every time. It has a significant effect on productivity. At the same time, it increases inventory, one of the wastes of Lean Manufacturing.
Batching is suitable when:
- The machine capacity is fixed
- The raw material is also in batches
- There is only one machine available that needs regular setup activities
Single Minute Exchange of Dies (SMED)
Depending on the type of industry, setups are often necessary to add flexibility to the production line. However, setups also waste a considerable amount of time. For example, changing tools in a press line takes a lot of time as they tend to weigh tons.
This lean manufacturing technique aims to reduce set-up times to less than 10 minutes by following these steps:
- Measure total changeover time
- Determine internal and external steps
- Move external steps outside of the changeover
- Shorten internal steps
- Improve external steps
- Standardise new changeover procedure
There are several benefits in applying SMED. It improves capacity, increases batch sizes without additional inventory investments, reduces overall process flow time and increases flexibility.
Total Productive Maintenance (TPM)
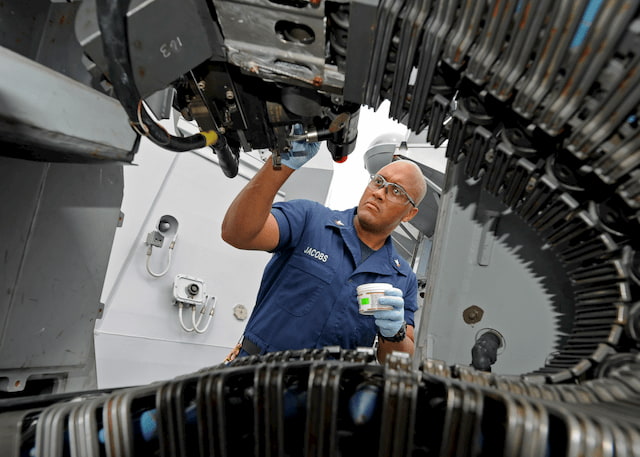
This Lean Manufacturing technique is an organisation-wide effort to reduce waste resulting from equipment failure, slower production speeds and defects.
The main objectives of total productive maintenance are to:
- Achieve maximum equipment efficiency
- Develop maintenance skills for all employees
- Increase equipment reliability
- Improve the efficiency of maintenance management
- Avoid unplanned machine downtime
- Optimise quality costs related to machine failure
Overall Equipment Effectiveness (OEE)
This is a key metric and tool to manage equipment-intensive production processes. It measures a system’s productivity
- How available a process is
- How fast a process is
- The quality of a process to produce defect-free parts
By doing so, the technique enables a systematic and detailed monitoring of waste. This includes wasted time and defects. Thus, it helps to identify small losses that may develop into significant losses over a longer time period.
Just-in-time (JIT)
It refers to producing only what is needed, when it is needed and in the needed quantity. One should enforce this throughout the production process.
Just-in-Time is one of the key elements of quantity control in lean production. But there are certain requirements, such as a very stable production system without excessive burden.
The main benefits include reduced inventory, reduced flow time, faster identification of work process problems, reduced waiting times and improved continuous flow.
Workplace Visualisation
This is a core technique of Lean Production. It consists of making all the important information about the workplace clearly visible and understandable.
Workplace visualisation includes what is done, how it is done, the current status, where things belong, etc. All this information is necessary to improve communication throughout the company.
Andon
This Lean Manufacturing tool is closely related to workplace visualisation. It involves using visual support and sometimes also audio alarms. Examples are screens to show production status, lights to draw attention to problems and other types of visual help to reduce waste.
The system encompasses a way to stop production to resolve a problem. The activation process can be automated or manual. For example, a worker may push a safety button to seize the production line.
Accumulated data about errors is then available for continual improvement in the workplace.
5S
5s is one of the most popular Lean Manufacturing techniques, it is also one of the tools to achieve workplace visualisation. The 5S are:
- Sort – sort through all inventory and remove unnecessary items
- Set in order – put all the items in the right place regarding functionality
- Shine – inspect all the machinery and maintain it regularly
- Standardise – standardised work helps to keep everything in order
- Sustain – make it a habit, so no one needs guidance
5S is one of the just-in-time manufacturing concepts that originates from Japan. This Lean Manufacturing tool is something more than just housekeeping. It is a systematic and sustainable method to organise the workplace.
The reduction of waste is achieved by maximising efficiency while improving morale and motivation.
Heijunka
This Lean Manufacturing tool is also known as levelling or production scheduling. Heijunka presents a different approach to normal productive process scheduling. The approach is to optimise the size of the batches in a batch production system. The goal is to achieve a continuous flow in production.
This is recommended when production needs to be very flexible and an even distribution of the delivery schedule is required. The main benefit is a reduction in lead times and inventory.
Companies with a steady influx of orders may adopt that method. Rather than producing 2 machines on Tuesday and 6 on Wednesday, it may be better to manufacture 4 on both days. Of course, this requires some previous data on order volumes.
Kanban
Kanban is the Japanese word for visual card. It refers to the use of visual cards to create a system of signals. Kanban improves the flow of materials and products in the factory and to the suppliers and customers. This helps to reduce waste from inventory and overproduction.
Today, many manufacturers are turning to electronic kanban solutions. It eliminates the problems such as manual entry errors and lost cards. IoT systems within a manufacturing plant are the Industry 4.0’s equivalent of the kanban method. They make for a great next step after seeing productivity increase through traditional kanban.
Poka-yoke
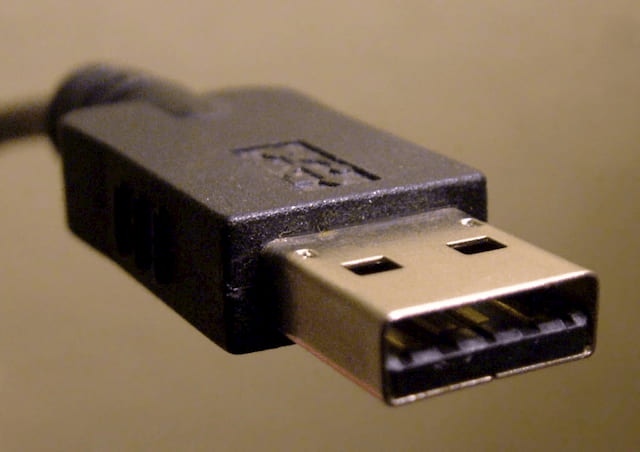
Poka-yoke is another Lean Manufacturing technique. The name derives from baka-yoke, meaning fool-proofing or idiot-proofing. The aim of this method is mistake-proofing.
A simple example of fool-proofing is the need to press the clutch when starting a car with a manual gearbox. This eliminates the risk of someone crashing a car just after ignition because it was already in gear.
Three ways to introduce poka-yoke for manufacturing:
- The contact method. Identifies mistakes and defects by testing a product’s physical attributes like shape, size, etc.
- The fixed-value method. A machine operator receives a message when the required number of movements are not made.
- The motion-step method. Makes sure if the correct steps have been made in the manufacturing process.
Looking to Start with Maximising Efficiency?
Choose any of the methods described above. You can start by implementing them step-by-step and see how it affects efficiency at the workplace. Lean Manufacturing methods are part of a larger picture to maximise efficiency at every stage of the product development process.
The ideas align well with concurrent engineering principles, so using the two hand-in-hand can have a substantial effect on the overall costs in terms of both money and time.
For engineering companies looking for innovative and efficient solution, we would also advise to look into cloud manufacturing. This helps to reduce the overhead costs related to procurement processes and does not need any investments.