Although Design for Assembly (DFA) and Design for Manufacturing (DFM) principles are often looked at as one subject and combined into Design for Manufacturing and Assembly (DFMA), they are separate methodologies.
Design for Assembly, a part of the Design for X (DFX) family, is the optimisation of the product and the assembly process, while Design for Manufacturing focuses on materials selection and manufacturing processes.
Over 70% of the product’s final cost is determined during the design process and the remaining 30% during manufacturing. Addressing potential issues at those early stages of product development will help you to get it right the first time or at least require less prototyping and fewer product iterations.
- Design for Assembly simplifies product design by reducing the number of components and minimising assembly steps, making manufacturing faster, cheaper, and more consistent.
- DFA key principles include standardising parts, incorporating modular design, and using built-in fasteners streamline assembly, reducing costs and minimising errors.
- Designing for symmetry and applying mistake-proofing techniques such as poka-yoke improve assembly efficiency and prevent incorrect part orientation.
- Considering assembly constraints early in the design process enhances manufacturability, lowers production costs, and improves overall product reliability.
What Is Design for Assembly?
Design for Assembly (DFA), simplifies the product’s structure by reducing the number of components and minimising the number of assembly operations required. The aim is to make the manufacturing process easier, faster and more consistent, therefore more productive.
The basic Design for Assembly process involves asking three questions for each part in an assembly:
- Does the part have to move relative to other parts in the assembly?
- Is the part made of different material for aesthetic or functional reasons?
- Does the part have to be separate to guarantee access to other parts or to be able to carry out repair and maintenance?
When answering no to all of the questions above, the part should most likely be combined with another part in the assembly.
Manual & Automated Assembly
Most products are assembled manually and the original DFA methods for manual assembly had an enormous impact on productivity. It was quickly realised that the most important aspect in optimising for Design for Assembly was keeping the number of components to a minimum and removing unnecessary features that do not add to the functionality of the product.
Different forms of guidelines to help designers were proposed in the 60s and 70s, but it wasn’t until the late 1970s that numerical evaluation methods were developed. This made estimating the time and cost difference between manual and automatic assembly easier.
The key principles for both manual and automatic assembly are similar. There are some differences though, since compared to a human, robots are quite limited in their motion range and capabilities. In Design for Automated Assembly (DFAA), a lot of the focus shifts to different tools and grippers that can be fitted onto robots, like vacuum cups, parallel grippers, three-finger grippers and electro-magnets.
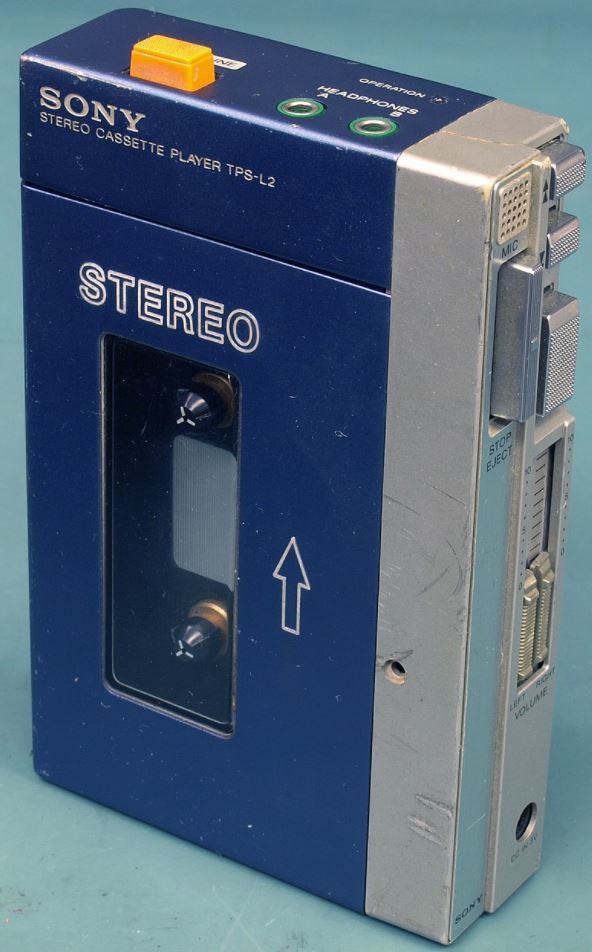
You should aim to minimise the need for reorientation during assembly with both manual and automated assembly processes, but it is particularly crucial for automation. The success story of Sony Walkman is a good example of assembly automation, incorporating single-axis assembly with only straight down moves (Top-down assembly).
When following Design for Assembly guidelines with more complex assemblies, it might not be always possible to eliminate reorientation completely, but try to bring it to a minimum.
- Personal account manager
- Quality assurance
- Payment terms for companies
- On-time delivery by Fractory
Design for Assembly (DFA) principles
The main principles of DFA to keep in mind are the following:
- Minimising part count
- Modularity
- Built-in fasteners
- Part symmetry
- Mistake-proofing
- Use of standard parts
- Use of reasonable tolerances
Considering all these aspects throughout the product development phase will ensure lower overall manufacturing costs, in turn, increasing the potential revenue. While DFA may seem very much producer-centric, many of these features will also be appreciated by the end customer.
So let’s dive deeper into each point to establish a common understanding that can help you on the way to build better products.
Minimising Part Count
The total number of parts in a product is a key indicator of design quality. Good products actually have fewer parts and they usually end up being more durable and easier to manufacture and repair. Keeping your part inventory as low as possible will help to cut down on assembly time and therefore on assembly costs. Less different components will prevent confusion resulting in fewer assembly problems.
But keep in mind that overly complex components might also have an undesired effect on manufacturing costs. When implementing Design for Assembly principles, communication between designers and other departments is the key to determining the most cost-effective alternative.
Modular Design
Incorporating modular assemblies into your production can be one of the biggest time-savers, especially if you have a range of similar products. Modular design also has secondary benefits as they are often easier to repair and customise, in effect increasing their utility and life cycle.
Built-In Fasteners
Different types of fasteners, such as screws, rivets and bolts, should always be considered as a target for designing out. Although fasteners are rather inexpensive on their own, the installation process is really time-consuming. In addition, threaded fasteners are known for being the cause of the majority of assembly line defects.
Incorporate fasteners into product design to speed up the assembly. Built-in fasteners like snap fits and adhesive fasteners often don’t require any special production equipment and make assembling easier.
It might not always be possible to get rid of fasteners completely, but for ease of assembly, try to use a minimal amount of different types and sizes. Ideally, you should aim to use common parts and the same tools not just for the entire assembly, but for the whole product line.
Symmetry
Creating a symmetric design reduces the time needed for reorientation. Make components fit either way around, so the assembly worker does not have to spend time figuring out the correct way to insert a part. If that is not possible, go the other way around and make asymmetry obvious.
Mistake-Proofing (Poka-Yoke)
Use poka-yoke principles in the form of physical obstructions to stop components from being fitted wrongly. Even adding a simple notch to your part will make it easier to identify and assemble. Making sure that a part can not be assembled incorrectly will avoid many problems down the line.
Use Commercially Available Standardised Parts
Reducing the amount of custom machining and fabrication made in-house and incorporating commercial off-the-shelf (COTS) products into your product design can save you a lot of time and money. Some examples include motors, gears, springs, enclosures, etc.
This will not only reduce assembly costs in manufacturing but also helps to speed up the product design process with fewer parts to focus on.
Keep Tolerances Realistic
Although with modern mechanical engineering equipment it’s possible to manufacture parts with extremely precise tolerances, it does not mean it’s always necessary.
Precision machining takes more time and drives up the production cost. Having too tight tolerances can cause potential assembly problems, even if the parts end up being just slightly out of specification.
Assembly Process Considerations
Avoid too small or too large components and provide your parts with features that make it easier to grasp, move, orient and insert them. Using self-aligning and self-locating parts and features in your product design can speed up the assembly significantly. Sometimes adding just a small chamfer or a dimple to your design can make a huge difference.
Be mindful of certain types of elements (springs, cup-shaped objects, etc.) that are known to tangle and jam together. When an assembly worker has to spend time untangling or separating nested parts, it wastes money and potential.
Conclusion
Combining the different practices of DFX can have a significant impact on the overall costs. Just imagine the accumulated benefits of Design for Manufacturing, Design for Assembly, Design for Cost and Design for Supply Chain.
While keeping all the different “rules” and advice in mind during the design phase might seem like an insurmountable task, most of the principles from DFX align to create a wholesome process. Many of the principles outlined in one overlap with others, as the methodology is universally helpful in many areas of product design.