When metallic components come out of manufacturing or fabrication, they generally require some type of surface finishing process to improve their appearance or corrosion resistance properties.
Sometimes, these treatments may also improve the electrical or mechanical properties of the part. This is an important stage in manufacturing and can have a significant effect on the durability and functionality of a part.
In this article, we cover one such process: electropolishing. We shall explore what it is, how it works and its advantages over other treatment methods. Let’s begin.
What Is Electropolishing?
Electropolishing, or anodic polishing, is an electrochemical process that uses electricity to remove a thin layer from the surface of electrically conductive metals. The removal of this thin layer improves the metal’s surface roughness as well as its corrosion resistance. The finished products look shiny and clean as the discolouration and/or embedded foreign materials from previous processes are eliminated.
Electropolishing can remove up to 40 micrometres from a surface, depending on the process parameters. But typically, electropolishing is used to remove between 8 and 20 micrometres.
There are applications where a very small amount of metal removal is necessary. Hypodermic needles are a good example. For such parts, a flash electrolytic polishing process can deburr edges and passivate the parts using a small amount of current and a short process duration.
The percentage of surface finish achieved depends on the initial finish. Up to 50% Ra (Roughness average) reduction is possible through electropolishing. But due to practical limitations, we can usually achieve between 25 and 40%.
However, as the Ra value becomes smaller, we get a diminishing rate of return. This means that a well-finished part will not be able to benefit in the same manner from electropolishing as a relatively rougher part. For instance, if we were to electropolish a metal surface that has Ra value of 10–15, we would only be able to achieve a reduction of about 10 percent.
The electropolishing process is also frequently used as a secondary finishing process to supplement mechanical polishing. Where mechanical polishing methods remove macroscopic surface imperfections, electropolishing removes microscopic surface imperfections.
For example, a 70 Ra part can benefit by about 40% if we were to use electropolishing right away, bringing the final Ra value to about 40. But we can use mechanical polishing first and reduce the Ra value to 40, followed by a 40% reduction from electropolishing to achieve a final Ra of about 20–25.
How Does the Electropolishing Process Work?
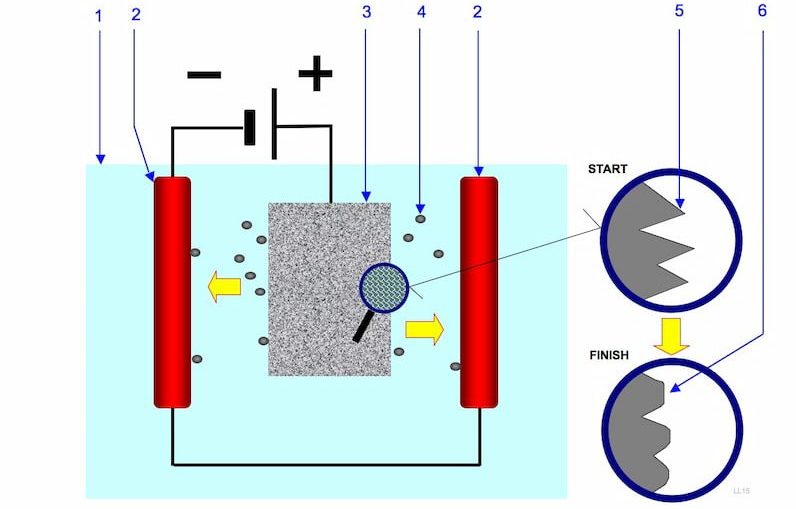
The electropolishing process works on the principle of an electrolytic cell. In the electropolishing process, we connect the workpiece to the positive terminal of the cell and make it the anode.
A suitable metal connected to the negative terminal becomes the cathode. The cell in this case is usually a DC rectifier that converts AC supply to DC supply at the output.
Let us understand the electropolishing process by dividing it into three distinct stages. These are:
-
Surface preparation
-
Electrolytic polishing
-
Post-treatment
Surface Preparation
Electropolishing requires a clean surface to enable a uniform electrical current. Contaminants cause uneven current density that will lead to uneven surface erosion.
But the surface can collect contaminants from previous processes or part handling in the shop. These could be grease, oil, shop dirt, fingerprints or any films left on the part after manufacturing. The amount of contaminants directly determines the final finish quality.
Thus, the first step is to thoroughly clean the surface of all contaminants. The cleaning process begins with an alkaline and solvent cleaner, followed by pickling. After each process, the part is rinsed to remove the process residues.
Electrolytic Polishing
The material to be polished is connected to the positive terminal (anode), and a different suitable metal is connected to the negative terminal (cathode).
The anode and cathode are dipped together in a suitable electrolyte solution. At the positive electrode, the material develops a positive charge, oxidises, and dissolves into the electrolyte. Burrs and corners have increased current density.
This step removes material at the microscopic level. We can finely control the thickness of the removed layer.
The following factors affect the removed layer’s thickness and the final surface quality:
-
Metal and electrolyte composition
-
Surface contamination
-
Electrolyte temperature
-
Current density
-
The specific gravity of the electrolyte
-
Electrolyte agitation method
Post-treatment
The electropolishing process also leads to a number of unintended reactions. The byproducts of these reactions deposit on the metal surface and must be cleaned to achieve a satisfactory end product.
Failure to clean these will cause problems such as inconsistency, corrosion and staining throughout service. In the case of stainless steel finishes, a nitric acid treatment followed by hot rinsing is used for post-treatment.
Electropolishing vs Electroplating
If you think about it, electropolishing is the direct opposite of the electroplating process. In the electroplating process, we deposit a thin layer of one metal onto another through an electrochemical reaction. The metal to be coated becomes the cathode, and the deposition metal becomes the anode. Thus, the anode dissolves and gets coated on the cathode.
In the electropolishing process, since we want to remove a thin layer, we make it the anode by connecting our workpiece to the positive terminal of the cell. Thus, the electropolishing process is also known as the reverse plating process.
The electropolishing process is also sometimes compared to the passivation process. But neither natural nor chemical passivation involves the use of electricity to form the protective layer.
- Personal account manager
- Quality assurance
- Payment terms for companies
- On-time delivery by Fractory
Applications of Electropolishing
Electropolishing is a cost-effective and versatile surface treatment process. When it comes to materials, electropolishing works with a long list of metals.
Some of the popular ones among these are aluminium, brass, copper, molybdenum, nickel, titanium, tungsten and zirconium. It also works with nickel, cobalt and copper alloys. Cast iron also benefits from electropolishing, although not much. Electropolishing carbon steels to deburr and improve the surface finish before plating is also common.
But perhaps the greatest use of the process is to electropolish stainless steel. Especially the 300 and 400 series stainless steels.
Electropolishing is essential to many industries. Let us take a look at a few of these.
Medical industry
In the medical industry, electropolishing is used to reliably clean and sterilise surgical instruments. Deburring surgical instruments before putting them into use is also necessary, as otherwise the parts may break off and harm patients.
Moreover, electropolished surfaces resist bacteria growth and have unmatched precision, which makes them highly biocompatible. The improved corrosion resistance is also a plus for surgical tools.
Automotive manufacturing
Electropolished pipes, gears and fuel lines reduce friction and improve the performance and durability of parts.
On the exterior, electropolishing can provide shinier and smoother rims, grills, exhaust components and runners that resist corrosion and last a long time.
Process equipment
A lot of industrial process equipment, such as heat exchangers, reactor vessels, mixers, storage tanks and pipes, benefit from electropolishing.
It reduces friction, corrosion and surface stresses while improving heat transfer efficiency, flow quality, durability and cleaning capacity. Electropolished surfaces perform as well as glass surfaces in many applications.
Apart from these aforementioned sectors, electropolished parts are extensively used in the aerospace, food and beverage processing, nuclear, clean room, semiconductor, water treatment and home appliance industries.Â
Benefits of Electropolishing
As seen in earlier sections, electropolishing provides a host of benefits in different applications. Through it, we can improve the function, finish, fit and durability of most metal parts. Let us look at how this happens by discussing its benefits. Some of these are as follows:
-
Eliminates surface defects
-
Reduces surface roughness
-
Works with complex surface topography
-
Improves corrosion resistance
-
Fatigue life improvement
-
Ultraclean parts with a decorative appearance
-
Bacteria-resistant surface
Eliminates surface defects
The process is highly effective at clearing surface defects such as fissures, cracks, micro burrs, abrasions, stains, weld discolouration and peeling. By dissolving the outermost layer of a part, most surface defects are smoothed over or eliminated.
Reduces surface roughness
Electropolishing removes metal from the micro peaks on a rough surface faster than it removes metal from recesses (anodic leveling). This reduces their height and makes the overall surface smoother. Targeted electropolishing can reduce surface roughness by up to 50%.
Works with complex surface topography
Being able to work with complex geometries is one of the most attractive features of electropolishing. While it is possible to improve the surface finish and lustre of flat parts by mechanical polishing, doing the same for complex geometries is always a challenge.
But with electropolishing, it is possible to remove equal thickness from the part throughout the surface. This includes recesses and interior channels.
Improves corrosion resistance
Stainless steel has the unique ability to form a passive film to resist corrosion. This phenomenon is known as passivation. However, this film is not enough to endure corrosion in environments that contain seawater or other corrosive chemicals.
Electropolishing can improve the corrosion resistance of stainless steel parts by up to 30 times more than passivation.
Fatigue life improvement
Electropolishing can also improve the fatigue life of parts. Parts that stretch, flex, bend or twist in a cyclic sequence benefit from electropolishing in the following way.
Each part that comes out of manufacturing invariably has some defects. If these defects are in the form of notches, pits, fissures or cracks on the surface, fatigue loading further exacerbates their condition, leading to failure.
By electropolishing these parts, we eliminate or minimise the effect of these surface defects. Their contribution to crack initiation and propagation is reduced, which results in a longer fatigue life for these components.
Ultraclean parts with a decorative appearance
Electropolishing strips the metal of its outer layer. This exposes the pure layer from underneath. Thus, the parts that come out of electropolishing are highly clean and aesthetically pleasing.
The process also removes any foreign material that may have become embedded in the metal workpiece during manufacturing or post-treatment.
Bacteria-resistant surface
Electropolished surfaces resist the growth of bacteria, especially when it comes to stainless steel. The altered electrical charge prevents bacterial growth and opens steel to a new set of applications.
Moreover, polished surfaces remove surface defects such as crevices and cavities, where bactericidal activity is normally not very effective.
Thus, electropolished steel can then be used in medical applications such as surgical instruments, implants, and prosthetics. It also allows the use of electropolished steel in food and hygiene-related applications.