Press brake tooling makes all the difference when choosing a manufacturer for metalworks. A variety of tools, along with the machinery’s tonnage, determines production flexibility.
Tooling both enables and limits production. If you make something out of the ordinary, there’s a good chance that special tooling is needed or it cannot be manufactured. Therefore, educating yourself on the topic can save you time and money. We will first start with the different types of bending punches.
Press Brake Punches
Knowing the types of sheet metal bending punches is the first step to understanding what can be manufactured. Although you may not be a specialist in bending, some background knowledge can help you with identifying impossible bends. Most of these punches actually achieve a variety of bends but each have their own advantages and specifics.
Standard Punch
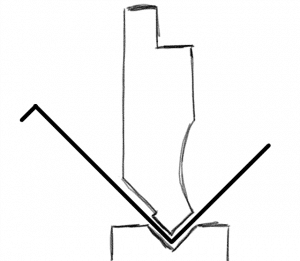
Standard punch is the most common bit of press brake tooling. It is used for air bending blunt corners or bottoming 90 degree ones. The standard punch has quite a stocky build, so it is able to take high loads needed for thicker metals or longer bending lines (check the tonnage chart in our sheet metal bending article).
Acute Punch
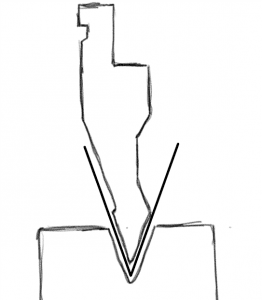
Acute punch is generally used to bend angles between 30…60 degrees. Again, the die’s thickness allows larger forces, so it is suitable for thicker materials. It’s also used to produce 30° angles before hemming. Then, the acute punch is switched for a hemming/flattening punch to finish the job.
You have to consider the mechanical properties of materials when designing your parts. For example, it is much more difficult to produce acute bends with some types of metals.
Narrow Punch
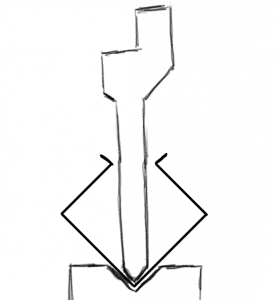
In essence, the narrow punch does the same job as a standard punch. The need for such a tool arises when there’s not much room for executing the final bend. In the example above you can see how the width of the die plays an important role.
Gooseneck Punch
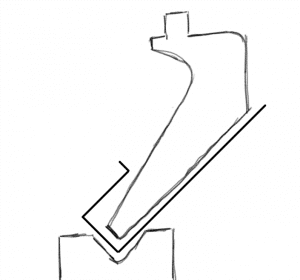
The gooseneck punch is used for your U-profiles. Therefore, it is a highly utilised tool but one has to understand the limitations.
A lot of people want to make U-profiles that have both of the sides high. You can see, looking at the picture above, that it is only possible to an extent. The punch widens towards the top and ends with a U-turn. So a wider base allows higher sides but there is still a limitation set by the punch’s shape.
Also, it is not as strong as your standard punch. Although it is quite sturdy, the force line is not supported for its way onto the workpiece.
Sash Punch
The sash punch is a little like a gooseneck punch – it makes bending around a corner possible. But it makes it possible so that there are angles on both sides of the bend. If you look at the picture and try to imagine making something like that with a gooseneck punch, you understand the necessity of such a press braking tool.
Press Brake Dies
Dies make up the second part of press brake tooling. Although from the outset, it’s mostly just V-grooves, there’s still some variety here as well.
1V Die
1V die or a single V press brake die is the most common type of die. It has a single groove that is suitable for certain angles and radii. If you need several different operations on one sheet, retooling is necessary if air bending doesn’t give enough flexibility.
2V Die
2V dies have two successive grooves. Thus, it allows continuous work without retooling, if a sheet has many similar bends that still have different tooling requirements. The grooves are close to the sides, making short flanges possible. The grooves have different widths and may have different angles as well.
- Personal account manager
- Quality assurance
- Payment terms for companies
- On-time delivery by Fractory
Multi V Press Brake Die
These are also known as press brake multi V dies. It has 4 different grooves on each side, meant for a variety of radii and material thicknesses. Still, you have to rotate the die to use another groove.
Another downside is that the groove is in the middle and the sides are not that short. Thus, it is not always suitable for short flange bending.
Still a very good addition to your press braking tooling inventory as it provides a lot of flexibility in one tool.
Rotary Die
Rotary dies allow similar bending capabilities to regular V bending but without damaging the material. The rotating inserts decrease friction – the material slides on the die surface instead of scraping along. Also, it leaves no marks like the the V die does.
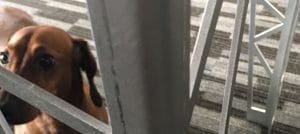
Hemming Die
Although definitely something that is necessary, it is just too uninteresting for a long description. So here’s a self-explanatory picture. It is for finishing the acute angle bends by flattening.
Offset Punch and Die
Those come as a set. It’s something that makes successive bending that much faster as they can be done in one operation. It also ensures that the bends are parallel as there is no room for dislocations.
Urethane Die
Another way to bend without leaving marks. The dies often have holes in them to allow easier force exertion in the wanted direction. Although it may be less accurate, it is still a good alternative when air bending because of the final surface quality.
Press Brake Tooling Length
There are standard lengths for both punches and dies. At first, it may seem something that an engineer really doesn’t have to know. That is not quite true though. Let’s say you have a 2000 mm metal sheet that has many small flanges or ears that need bending.
Now, you have made cutouts, so the press operator can bend those without touching the surrounding sheet. But your cutouts are 28 mm. Maybe you should think twice about the length of these. And for that, it is useful to know the standard lengths.
In this example, the only way is to choose 20 mm dies but that won’t guarantee the best possible quality. It’s always better to have the dies the exact length of the bending line. If possible, conform your design to standards.
Standard lengths for press brake dies:
835; 415; 370; 200; 100; 50; 40; 20; 15; 10 mm
Standard lengths for press brake punches:
835; 415; 370; 100; 50; 40; 20; 15; 10 mm
Looking for a good metal bending service? Look no further!