Design for Manufacturing is an emerging design philosophy under the Design for Excellence (DFX) ideology. DFX is a set of relatively new methods for managing design and production processes. These methods find more and more use in product design today due to their incredible benefits.
From the many methods under DFX, designers choose one or more that are relevant to their product design objectives. Then, by implementing the principles under each of those methods, the designers can ensure an excellent product design.
Design for Manufacturing (also known as Design For Manufacturability or DFM) is often confused with Design for Assembly, but in reality, they are separate methodologies. They can be combined into a single production method though, called Design for Manufacturing and Assembly (DFMA). In this article, we’ll be focusing on DFM, so let’s start from the beginning.
- Design for Manufacturing optimises product design by selecting the most suitable materials and manufacturing processes, ensuring easier and more cost-effective production.
- Early integration of DFM principles minimises manufacturability issues, reducing redesign costs and shortening time to market.
- Standardising components, simplifying designs, and avoiding unnecessary complexity improve production efficiency and lower overall costs.
- DFM enhances collaboration between designers and manufacturers, leading to higher quality products and a smoother manufacturing process.
What Is DFM?
Design for Manufacturability is a product design ideology that focuses on creating a better design at a lower cost by optimising the selection of materials and manufacturing processes. Following these guidelines, the final product should be easier to manufacture and the production should take less time when compared to the original design.
DFM helps us analyse the different aspects of design and manufacturing processes in the light of many prudent principles. It provides new ideas and techniques to bring about a positive change in product design to benefit all the involved parties (designer, manufacturer and customer).
Such an advanced manufacturing simulation was once a pipe dream due to the lack of available tools and manufacturing processes. This is no longer the case. Today, with advanced digital manufacturing simulation tools and low-cost fast manufacturing processes, such as additive manufacturing, it is easier to carry out extensive simulations and even create physical iterations for specific products.
These tools enable deep DFM modeling and real-world testing at a fraction of the original cost. Thus, an increasing number of manufacturers are integrating DFM into their organisations to reap its many benefits.
DFM Applications
There is a range of reasons why DFM is so invaluable in the competitive markets of the present day. Let’s take a look at how following DFM principles can result in an efficient design and manufacturing setup. With DFM, we can:
- Build realistic cost models in line with product objectives
- Minimise manufacturability issues so that the product can be manufactured quicker and in a more economical way
- Create an efficient design that leaves room for potential design changes in the later stages without a huge cost.
- Ascertain unnecessary design features that add costs and eliminate them
- Drive down supplier bids by modifying the design using DFM principles
DFM Principles
In this section, we shall learn about the different avenues on which the designer must focus when creating a DFM-friendly product. Optimising each one of those areas will ensure that the product, as a whole, becomes the very best version of itself. These five focus areas are:
- Manufacturing process
- Product design
- Product material
- Service environment
- Testing and compliance with various standards
Manufacturing Process
Using the right manufacturing process is critical to the success of the product. One needs to assess several factors such as the cost, product material, volume, surface finish, post-processing needs and tolerances to select the most appropriate manufacturing process for the product.
For example, choosing injection moulding for products that will be produced in small volumes is not sustainable due to the huge upfront investments and overheads. In such cases, one may prefer additive manufacturing or thermoforming processes. These processes enable cheaper manufacturing with fewer parts rather than having to make a huge investment in moulds and tools.
It is imperative that the company finalises the manufacturing processes as soon as possible as the remaining four factors are highly dependant on it. The product design may suggest multiple options for manufacturing processes. Each of these choices must be analyzed using DFM principles for an optimum selection. The overall viability must be used as a deciding factor instead of the manufacturing cost. It may be that a manufacturing process has a low production cost compared to another but the overall costs may rack up significantly during distribution etc.
Another aspect that can have a huge impact on the final product cost is the tolerances assigned to the product. Specifying unnecessarily tight tolerances can increase the costs in the form of extra machining time or it might add the need for a secondary machining process. At times, the company may have to change the manufacturing process to meet certain specifications. The designers should set the loosest tolerances possible while meeting the functional requirements of the product. Using such tolerances reduces tooling costs and the number of defects, all while making the product easier to manufacture.
Product Design
Product design is probably one of the key factors that has significant implications on the feasibility of the operation. An efficient design can cut down costs and lead times remarkably, sometimes through seemingly minor modifications. However, the opposite can be true as well. A lot can go wrong when designers don’t understand manufacturing. This is why designers need DFM tools to analyse the effects of their design choices on production.
Take the example of a plastic product designed with different wall thicknesses. At first glance, it may seem like a wise decision to cut down on raw material costs wherever possible, as long as the desired strength is not compromised. But when this decision is evaluated in the light of difficulties involved with manufacturing a plastic product with varying thickness, we soon discover that it would be far more feasible to maintain a uniform thickness. This is understood by any engineer worth his salt but may not be so clear to designers that create product prototypes.
Product Material
The engineers must select the raw material, its grade and form early on in the product development process. This selection depends on the expectations from the product. Several aspects such as strength, thermal/electrical resistance, surface finish, flammability, opacity and machinability guide the engineers towards the suitable choice. As the material gets harder, its machinability reduces. In addition to choosing the right metal, material grade and form can also have a significant impact on the final part cost.
By form, we mean the shape and size of the raw material before machining. Metals, for instance, can be supplied as plates, bar stocks, strips and sheets. Usually, more than one form can be used but their rates and properties differ. For example, bar stock of aluminium costs about half of the price of an aluminium plate on a weight basis. It is important to evaluate how preferring one raw material form over another affects the grand scheme of things.
- Personal account manager
- Quality assurance
- Payment terms for companies
- On-time delivery by Fractory
Service Environment
One of the steps in an effective DFM process is to evaluate the service environment to create a functional product at low production costs. A product that is supposed to work in a dusty area is not built up to the same specifications as one that will work underwater. DFM suggests aiming for product quality in line with the normal working conditions of the product. The intensity and effect of environmental factors such as rain, snow, wind, salt, moisture and abrasives must be considered during DFM process.
It is important to distinguish between realistic and unrealistic expectations to reduce manufacturing costs. A product that will be used only in dry areas over its lifetime does not need marine-grade specifications. For instance, the 5083 marine-grade aluminium is a must for marine applications due to its superior corrosion resistance properties, but using this grade in environments with a medium-to-low chance of corrosion would not be rational. During DFM, we only consider normal operating conditions to eliminate unnecessary manufacturing costs.
Testing and Compliance With Various Standards
While carrying out DFM, manufacturing engineers must always keep testing and compliance requirements at the back of their minds to prevent any hiccups in later stages. A product that can be manufactured at a fraction of the original cost but cannot pass certifications will never reach the market.
There are various types of standards for certifications. They can be industry standards, third-party standards, or even standards set by the company itself to ensure a quality product. For many products, regulatory agencies may also set the relevant standards. Complying with all of these standards requires the manufacturer to have testing capabilities for all of them.
When following DFM procedures it is recommended to test the product design for compliance before mass production begins. Waiting until the very end of the product development process can bring huge costs and may even require the product to be taken back to the design stage. Where applicable, it is recommended to use non-destructive testing methods since the test piece will still be fully operational and intact even after completing the testing process.
Key Benefits
Any company that invests in DFM will most likely find poor design and manufacturing decisions in their products that could have been easily avoided. Some key benefits of DFM are as follows:
- Cost reduction (increased profits)
- Shorter time to market
- Improved product quality
- Streamlined product development process
- Smoother manufacturing process
- Easier to scale up production
Cost Reduction
Design for Manufacturability can significantly reduce production costs. Such a cost-effective operation can in turn improve profitability by increasing the ROI. Alternatively, the manufacturing companies may transfer the benefit of low cost to the customers in a competitive market.
Shorter Time to Market
As most of the design and manufacturing issues are addressed in the early stages of the design process, fewer issues crop up during the actual manufacturing process. In effect, it is less time-consuming, which improves the time-to-market for a new product.
Improved Product Quality
Design for manufacturability ensures that the product meets the quality standards set in the design phase. It makes sure that the performance, surface finish, tolerances, reliability, aesthetics, conformance, features, durability, serviceability and perceived quality of the product match the target specifications.
Streamlined Product Development Process
Design for Manufacturing starts with the big picture in mind. It clearly defines the part’s design, final quality, manufacturing processes, component materials, ease of distribution, etc. which leads to an extremely well-managed production process that takes all aspects into account. Thus, designing products using DFM creates a solid plan for product development before the design process even begins.
Smoother Manufacturing Process
This is the ultimate goal of Design for Manufacturability. Due to in-depth planning of the manufacturing process, the manufacturing companies and/or the contract manufacturer are clear on the deliverables, leading to a smooth production setup. For instance, instead of depending on the manufacturer to calculate the cartesian coordinates for CNC machining, the coordinates for all features can be shown in detail on drawings.
Easier to Scale Up Production
An effective Design for Manufacturability process ensures that when the time comes to increase production levels the manufacturing setup is easy to scale up. Following the guidelines makes sure that the components used in the assembly can be sourced with ease and that the production line is capable of delivering an uninterrupted manufacturing and assembly process even with the increased quantities.
How to Implement
Design for Manufacturing is a great way to save costs while delivering a premium product, but how exactly can companies get started with it? Implementing DFM can be a challenging undertaking for most organisations but it does not necessarily have to be like that. In this section, we shall see how organisations can integrate DFM in three simple stages.
Early Integration
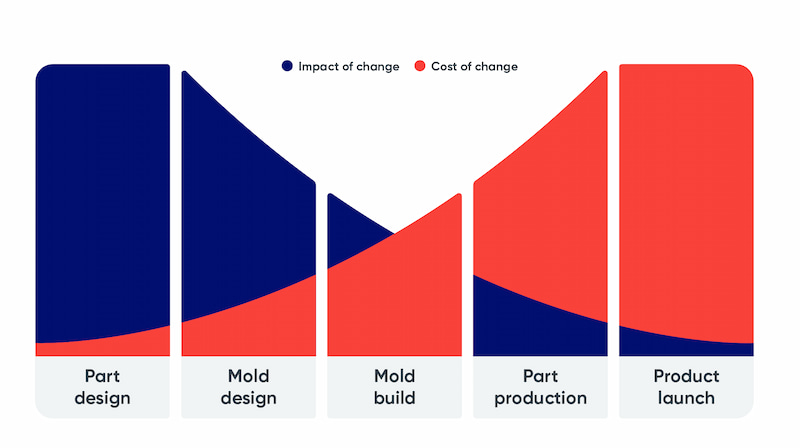
Engineering companies must integrate DFM in the early stages of their design process. This is the best time to work out any redesigns. Making design changes later can be extremely difficult and come with a hefty price tag, especially when different tooling is needed for the new design. Manufacturability evaluations must be carried out in the early stages as thoroughly as possible.
Identify Opportunities for DFM Techniques
A good DFM evaluation of the current design and manufacturing operations should expose many avenues for improvement. When manufacturing specialists cooperate with designers, they are able to identify wastage in manufacturing and provide suggestions for more efficient and sustainable alternatives.
The specialists can also work with suppliers and understand the constraints which enable them to suggest optimal design decisions to improve the manufacturability of the setup in the early stages Today, as OEMs are increasingly outsourcing manufacturing to faraway locations, such DFM interventions are becoming more and more critical to ensure a profitable system.
Broaden DFM Scope
As manufacturing becomes more efficient over time, the company can turn its attention to other aspects that have an effect on the manufacturability of the product by broadening the scope of DFM. Factors such as product dimensions and weight, tooling costs, scrap reduction, labor costs, overheads, etc. can all be optimised using DFM techniques. These factors affect the product cost structure directly and optimising these areas can improve the overall efficiency of the organization.
DFM vs DFA
DFA stands for Design For Assembly and refers to the optimization of the product itself and the assembly process to reduce cost, effort and time. Let’s see what are the main differences between DFM and DFA.
Focus Area
DFM focuses on reducing the required number of manufacturing operations while still meeting the product’s functional requirements. It also aims at reducing the complexity of the operations and using cheaper and readily available materials and processes wherever possible.
For instance, if a hole can be cast, pierced or molded with adequate accuracy, the designers should avoid drilling. Boring is even more expensive than drilling. Thus, when drilling can get the job done, boring must be avoided. The aim is to make production as simple as possible by sourcing and producing parts efficiently.
In Design for Assembly, the designers must always keep the ease of assembly in mind. Simplifying assembly steps will reduce the costs, effort and time put into a product. For instance, reducing the total number of parts in the assembly and designing out fasteners will speed up the assembly process significantly and increase the overall efficiency. Another key factor to avoid problems down the line is to reduce the probability of incorrect assembly by carefully designing individual components so that they can only fit in a specific orientation (mistake-proofing).
DFMA
From the merger of DFM and DFA, a third discipline known as Design For Manufacturing and Assembly was born. When comparing DFM and DFA techniques side by side, there’s a lot that overlaps. Ultimately, the intention of both DFM and DFA is to ease the manufacturing process of a product. Both methodologies benefit from following design guidelines such as:
- The use of standard components
- Removal of unnecessary parts and features
- Incorporating a modular design
- Designing multi-functional parts
- Eliminating fasteners
DFMA applies these techniques to a company’s standard production line to create a product that is easy to manufacture and assemble. It may use integrated product development disciplines such as concurrent engineering to bring down costs and improve product reliability.
Conclusion
Over 70% of the product’s final cost is determined during the design stage. Engineers are left with very little wiggle room for cost reduction once the design is settled. DFX allows us to select a focus area for the design so that product objectives can be achieved. Design For Manufacturing in particular helps to achieve design simplicity and reduce manufacturing costs which usually account for the largest portion of investments for a company.
It provides a much-needed edge for engineering companies in today’s competitive market. It is easy to overlook DFM due to the lack of information, but research and case studies have shown that the proper application of DFM principles can guarantee stellar results.