Design for Sustainability is an offset of the Design for X (Design for Excellence) philosophy. DFX encompasses a wide range of methodologies to improve product design and manufacturing processes. The ‘X’ can be substituted to represent a certain aspect that is the central theme to the design and production process.
Typically, product designers select focus, for instance, Design for Manufacturing (DFM), Design for Assembly (DFA) and Design for Reliability (DFR), and optimise those aspects of the product. Every design decision is evaluated in the light of the selected focus and relevant changes are then made taking the full life cycle of the product into account. Combining these subcategories can have an even greater effect on the final product, a great example of this is Design for Manufacturing and Assembly (DFMA).
In this article, we shall learn about design for sustainability and discuss principles that can take us closer to achieving it.
What Is Design for Sustainability?
Design for Sustainability (also sometimes known as DfS and D4S) is a subset methodology under the DFX family with its main focus on developing sustainable products. Sustainability is the judicious use of natural resources in a way that does not compromise the future generation’s ability to use them.
Sustainability is an enormous topic that converges a wide variety of subjects and philosophies under its wing. All of the sustainability strategies have either one or both of the following objectives:
-
Use fewer resources
-
Prefer eco-friendly alternatives
These resources could mean raw materials, processes, systems, distribution methods and anything else that is necessary for a product to exist. If we take a closer look, it is clear that almost all of the resource choices for a product are affected by its design.
In other words, the design stage is the most influential in determining how a product will affect the environment through its raw materials, manufacture, distribution, usage, maintenance and disposal.
In fact, the Sustainable Product Policy by the European Commission states that as much as 80% of a product’s negative impact on the environment is finalised at the design stage. Therefore, it is of paramount importance to evaluate and minimise environmental impacts at the design stage itself. Design for Sustainability helps us to carry out a critical evaluation of all the different aspects and to arrive at an environmentally sound product.
The Need for Sustainable Design
Sustainability in production and in the use of products has become increasingly important in the past few decades. There has been a rise in awareness about the negative impacts of unchecked resource extraction and consumption since the dawn of the industrial revolution.
Such awareness can be attributed majorly to the improvement in measurement methods in recent years. These methods have allowed us to gather irreproachable data on resource depletion and environmental degradation. The numbers indicate that there is a pressing need for sustainable products so that future generations can also enjoy a high quality of life.
Without taking strong measures in favour of sustainability, we will likely run out of natural resources, many species will become extinct and the environment will be damaged irreparably. Consumers can make an environmental impact when preferring socially responsible products to minimise waste and their carbon footprint.
It is not right to shift all the responsibility to the end-user. Manufacturing companies and their designers have to take the responsibility for the environmental effects of their products and work actively on designing more sustainable products.
The Shift Towards a Circular Economy
Traditionally, the economy has followed a straight-line pattern. Resources are extracted from natural sources. They are then processed and transformed into products and shipped to consumers. After their use, they are sent to disposal sites where, except for precious metals, not much is extracted. Such a system is popularly known as the linear economy. This kind of system is highly unsustainable and needs to change.
A sustainable alternative to this system is the circular economy. The main focus of this type of economic model is to reintroduce used parts as raw materials for new products. The intent is to move from a high-waste to a high-value model. Such a system is highly resource-efficient and reduces the effect of consumer demand on the exploration, pollution, and wastage of natural resources. Models such as biomimicry, cradle-to-cradle, product service systems (PSS), 4Rs, are all strategies that can provide design features to achieve a circular economy.
The 4Rs in particular is a very effective tool in building a circular economy. It includes four principles that can be applied by almost every individual and have an exponential effect. These principles are:
-
Reduce
-
Reuse
-
Repair
-
Recycle
A good design can influence all of the 4Rs of a product. While the first three are somewhat easier to understand, let us see how recycling is gaining more and more traction in recent years. Using components made from recycled raw materials is considered a sustainable sourcing strategy in the circular economy.
Thanks to advances in technology, we are now able to recycle more types of waste in a cheap and effective manner. Materials such as plastic, wood, glass, cardboard, rubber etc, can be recycled into a wide range of products. Rubber tyres, for instance, can be granulated and used in railway ballast, speed breakers, driveways, high-strength concrete and in many other applications.
In addition to big brands such as Apple and Nike, many small businesses and startups are also introducing products manufactured from recycled commodities. These efforts are expediting the world’s journey towards a circular economy. It is important to note though, that the first three Rs have a bigger impact than recycling as they also save the fuel required by recycling machines.
- Personal account manager
- Quality assurance
- Payment terms for companies
- On-time delivery by Fractory
Design for Sustainability Principles
True sustainability may be impossible to achieve. In such a utopia, human efforts to meet the current generation’s demands would have a beneficial (or at least insignificant) effect on the environment’s capacity to provide them. Such a situation is practically impossible as the manufacture of any product results in loss of materials and energy in the form of material extraction, manufacturing and transportation.
Using appropriate strategies can, however, help us get closer to the concept of true sustainability. Some actionable sustainable design principles that can be implemented to create better designs are:
- Dematerialisation
- Modular design
- Prefer renewable energy
- Migration to product-service systems
- Design for longevity
- Limit or eliminate long-distance outsourcing
- Invest in simulation
Dematerialisation
Dematerialisation in a design process, as defined by the United Nations Environment Program (UNEP), is “the reduction of total material and energy throughput of any product and service, and thus the limitation of its environmental impact. This includes reduction of raw materials at the production stage, of energy and material inputs at the use stage, and of waste at the disposal stage.”
There are many ways to achieve this. One way of carrying out dematerialisation is the miniaturisation of the product. This results in greater profit margins as fewer and smaller product components are needed. A product with a smaller form also requires reduced packaging, storage area, transportation and delivery costs and minimises carbon emissions involved in each of the product life stages.
Packaging in particular is a major focal point for many brands. Switching to recyclable materials and for example adopting customised shrink sleeve labels rather than bulkier, more complex containers, ensures that they are aligned with sustainability standards and customer expectations inside and out.
A good example is how smartphones have discarded the original design with a physical keypad or how tablets have replaced laptops in many applications. They have achieved a smaller form over the years and have become more resource-efficient.
Similar efforts have been carried out in the automotive front to achieve higher fuel efficiency. The dematerialisation (or mass-optimisation) of car chassis, engines, brakes, tyres has improved fuel efficiency. Lower fuel consumption has in turn led to reduced emissions and environmental damage. Dematerialisation of machine tools and manufacturing systems is also underway. Further progress in these areas can potentially save several million tonnes of CO2 emissions and steel per year.
The digitalisation of services is another efficient method of dematerialisation. Designers can eliminate features and products that produce waste by creating an alternate way of accessing the same service. Common examples are e-readers for books, newspapers and magazines. Bill and taxes delivery by email instead of postal mail.
Modular design
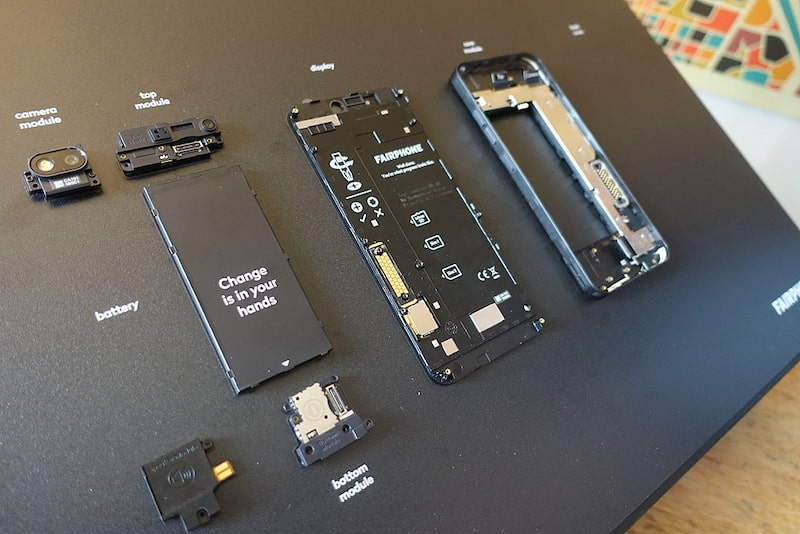
A modular design refers to the use of components as modules that can be used in multiple products. Modules are predesigned components with a specific function. The advantages include cheaper and easier manufacturing, assembly, replacement, repair and disposal.
For instance, a smartphone can have independent modules for the camera, GPS, power, storage, etc. When a component breaks, the individual module can be replaced instead of the full product. Such a design also provides a higher degree of customisation to the user.
On the sustainability front, modular designs control consumption rates and reduce waste production. Newer features and technology can be added to existing products as the modules can be swapped. A better camera can easily replace the original camera without having to buy a new phone. Many smartphone manufacturers are heading towards this. The Fairphone is a shining example of modular design.
Prefer renewable energy
Many products require constant or periodic energy supply to work. These products, known as active products, keep tapping into active energy systems for their function. Recent years have seen a shift towards electric drives, with the most notable examples coming from the automotive and shipbuilding industries.
Renewable energy can generate sufficient electricity for our needs. Designers must consider incorporating the use of renewable energy as the main or at least as an alternative energy source in their projects to achieve a more sustainable design.
Greater reliance on renewable alternatives, such as wind, solar power and hydroelectricity (instead of petrol, diesel, gas and coal), propel us towards sustainable development while allowing us to maintain similar energy usage levels.
Migration to product-service systems
Product service systems refer to a business model where the company provides services besides the product to improve their environmental performance and sales. In such systems, a company leases its products to the consumer instead of selling them for good.
They offer the function instead of the product. As the company still retains ownership, it can better control the distribution, use, maintenance and disposal of the product. Such a model compels companies to create durable, repurposable, remanufacturable, repairable and easily disposable products.
Traditionally, the responsibility of proper disposal has been left to the consumer. This provided little incentive for the manufacturer to design for efficient disposal. But in a product-service system, this responsibility is shared by the manufacturer and the consumer. This encourages the designers to opt for a sustainable design approach towards the full life cycle of the product, resulting in better resource efficiency and waste management. A great example of this practice is how IBM shifted to renting servers instead of selling units directly to customers.
Car-sharing services are another great example of a smart product-service system where the customers get to experience the benefits of temporary ownership of goods without the burden of actually owning them. Personal cars are the primary cause of problems in urban transport, they take up city space and cause congestion, using alternative transport options such as car-sharing offers many environmental benefits.
An increasing number of such car-sharing services have emerged, providing individuals with access to on-demand transport. Hailing from Estonia, Bolt is a prime example of this type of collaborative consumption model.
Design for longevity
One of the best ways to progress towards the sustainable use of resources is to extend the life of current products as much as possible. Designers have the power to maximise how long a product can be used through its design. Durable products can considerably relieve the pressure on the environment by reducing the amount of raw material and energy required to create new products.
Let’s explain this by taking a smartphone as an example. The results of a Eurobarometer survey (Kantar, 2020) indicated that 69% of users in the EU would like their mobile phones and tablets to last five years or more. But due to a degrading battery, most people are switched to switch their devices roughly after every two years. If designers were to improve the battery performance (or would embrace modularity), it would increase the likelihood of the product achieving its expected life of 5+ years as all other components still work fine at the end of two years.
The initial objective must be to create durable products. Special attention is needed for components that typically have a short life span. They should be able to handle normal wear and tear without breaking down.
For products that require regular maintenance, the ease of which maintenance can be carried out by the end-user is an important factor when ensuring a long service life. Ideally, the task shouldn’t be too complicated or costly. The product should also be easy to dismantle and assemble. Cost and ease of repair are equally important.
Using screws instead of glue and labelling internal components are some practices that can be used for this outcome. Although the use of screws might contradict the principles of some other methodologies from the DFX family (e.g. Design for Assembly suggests designing out the use of fasteners wherever possible). The key to success lies in efficiently combining these different methodologies to arrive at a result which makes sense for the product at hand. In this case, incorporating fasteners into product design might be a reasonable choice.
Another key consideration when designing for longevity is the evaluation of future upgradability and compatibility with past products.
Limit or eliminate long-distance outsourcing
Increasing shipping capacities have made freight more affordable. This has resulted in outsourcing manufacturing operations to countries with lower labour rates. Manufacturing/assembling products in the Pacific Rim countries, such as China, Japan and Korea, is usually cheaper even with the added costs of long-distance transportation.
The effect on the environment, however, is negative since the resources required to manufacture the product are the same either way but now we have added several tonnes of extra emissions due to the intercontinental transport. It is important to prefer local suppliers when designing for sustainability. Besides lowering the environmental impact, eliminating outsourcing would support local industries.
This aligns with Fractory’s principles: when offering laser cutting, CNC machining and other metal fabrication services we’re utilising the capacity and capabilities of regional suppliers.
Invest in simulation
CAD/CAM/CAE software offers great advantages in the product design and manufacturing stages. Today, computers can simulate a large range of products and scenarios, allowing us to customise every single aspect before raw materials even reach the shop floor. With 3D CAD software, we can create complex parts, assemblies and drawings eliminating the need for physical prototypes.
Using CAE (computer-aided engineering) software, we can analyse individual parts as well as entire assemblies for stresses, defects, impact, heat and fluid flow. We can even simulate tooling for manufacturing processes (e.g. forming) and shift things around assembly lines for optimisation.
Traditionally, many trial and error loops would be required to arrive at the most optimal design. But with simulation, all these loops can sometimes be completed in a matter of hours, saving precious resources in terms of raw materials, time and overhead energy costs related to electricity, water etc. It also reduces wastage as only a small number of products are out of spec when the part goes into actual production. Such a production method is, therefore, highly sustainable as well as profitable.
Another advantage of CAD is that it can be coupled easily with manufacturing equipment such as CNC machines, 3D printers etc. 3D printing, in particular, is highly resource-efficient owing to it being an additive manufacturing process. The material is added layer by layer to create a part unlike in a subtractive manufacturing process such as milling. Thus, 3D printing creates zero waste. Such an outcome is beneficial for the manufacturer, the customer and the society at large. Even when 3D printing is not always reasonable for mass production, 3D printed prototypes can always be used in testing procedures such as wind tunnel tests.
Sustainability at Fractory
Fractory aims to guide manufacturing to become more sustainable. Our mission is to streamline the procurement process by eliminating all the unnecessary steps. We’re not only focusing on the environmental aspects but we’re handling sustainability as a wider system that consists of three main pillars:
-
Environmental sustainability – is the responsibility to conserve natural resources and protect global ecosystems to support health and wellbeing, now and in the future. We aim for more efficient use of the available machinery and filling the production gaps by distributing jobs according to manufacturer availability, lead time, expertise, capabilities. Less material waste is created due to efficient job distribution and transportation miles are decreased by sourcing manufacturing locally, resulting in less CO2 released into the atmosphere.
-
Economic sustainability – means that decisions are made in the most equitable and fiscally sound way possible while keeping the other aspects of sustainability in mind. We strive to increase the economic sustainability of both customer and supplier businesses by creating an economically attractive cloud manufacturing platform, saving time of our clients and suppliers while also managing their risks regarding product quality, production capacity and transportation.
-
Social sustainability – is based on the concept that a decision promotes the betterment of society. In general, future generations should have the same or greater quality of life benefits as the current generation do. We strive to help the social cause by investing in education, creating awareness around engineering and manufacturing in general, engaging with the community and sharing our knowledge and resources.
Conclusion
Earth’s resource levels are plummeting at a fast rate, especially in the last few decades. These decades have seen both increased production and product waste. The amount of waste generation has increased manyfold with non-durable goods (products that last less than three years) making up for a greater portion compared to durable products.
For sustainable development, mindless mass consumption and throw-away culture need to be done away with. It will certainly take some time and thought on how to achieve this without damaging the economy. In the meantime, DFS can provide us with ways to ensure reasonable use of our resources and limit environmental degradation to regenerable levels.
An efficient DFS strategy must consider the whole life of the product rather than just the end of it. Due consideration to factors such as packaging can significantly reduce waste levels. Being directionally right is definitely a positive first step but the actual benefits of DFS will be seen only when we get the details right as well.