Electron beam welding is a process that utilises the heat from a high-velocity electron beam to form a weld. An electron gun generates the beam through the use of magnetic fields. The kinetic energy from electrons is converted to heat upon contact, thus melting the workpiece and creating a joint.
Let’s cover some key points that make electron beam welding stand out from other welding methods.
- Electron beam welding offers high precisionand deep weld penetration, making it ideal for complex and thick metal assemblies.
- EBW requires sophisticated machinery and skilled operators, leading to higher initial costs and maintenance demands.
- The process typically occurs in a vacuum chamber, ensuring clean, contamination-free welds.
- EBW is capable of joining dissimilar metals, making it versatile across various applications, including aerospace and automotive.
- The process is energy-efficient, converting up to 85% of electrical input into usable power.
What Is Electron Beam Welding?
Electron beam welding (EBW) uses a high-velocity beam of electrons to melt and fuse metals together. The electron beam can be focused to create a small weld area, which makes it ideal for welding delicate parts or complex designs. On top of that, EBW works at a rapid rate, making it one of the fastest processes in assembly welding.
Electron beam welding machines are quite complicated, requiring skilled operators to achieve optimal results. On the other hand, it offers a wide range of penetration depth, generally from 0.127 mm to 50 mm/0.005 to 2 inches (although much higher depth can be achieved for certain materials) when using a filler material with the latter, making it stand out compared to common welding techniques like MIG, TIG, and stick welding. EBW fusion welding process run on a single pass creates joints with minimal distortion and possesses the ability to join different metals.
Electron Beam Welding Process
The working principle behind electron beam welding is emitting a focused beam of high-velocity electrons into a joint. This process is usually performed inside a vacuum chamber to improve efficiency and prevent the electron beam from dispersing.
High voltages are supplied into an electron gun, which then expels a high-velocity stream of electrons with the help of cathodes, anodes, focusing coils, and magnetic fields. The intensity of electron beams is 100-1000 times higher than arc welding, allowing deep penetration and narrow heat-affected zones.
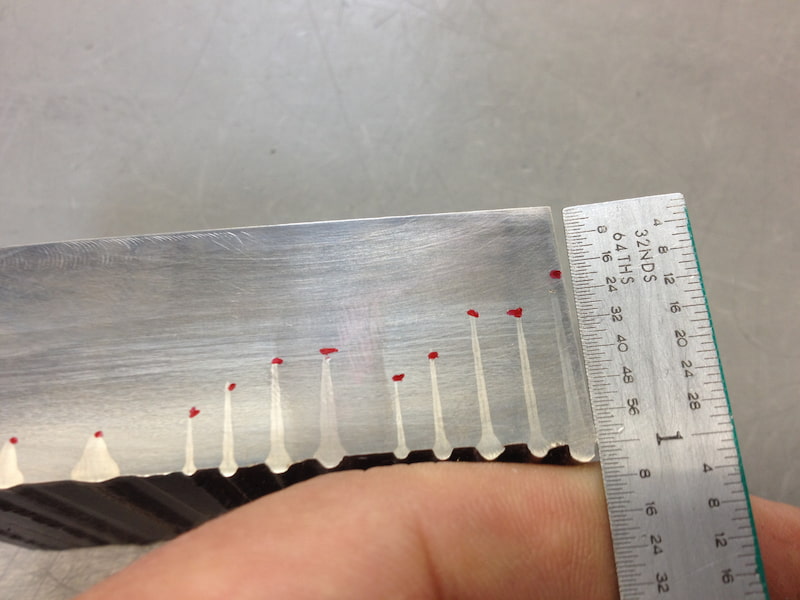
Similarly to plasma welding, the EBW process can be run in low power, medium power and high power aka keyhole mode. The low power mode is used to produce extremely fine welds, which can be as small as 20µm. Medium power is generally used for weld thicknesses from 1mm to 20mm, anything over that is in the domain of high power electron beam welding. Running the machine in keyhole mode can penetrate up to 300mm of steel and is known to create stable, good-quality welds for material thicknesses over 200mm.
Recent breakthroughs in EBW allow local welding with a workpiece larger than the vacuum chamber adding a bit more versatility to the welding process. This welding technology is achieved by having only the electron beam gun inside a vacuum box while the workpiece itself remains outside of the vacuum chamber.
Materials
The technology behind electron beam welding allows various metals to be welded together, including dissimilar metals, since it is mostly performed in a vacuum environment. EBW is mainly used with these materials:
-
Bronze
-
Cobalt alloys
-
Copper
-
Hastalloy
-
Inconel
-
Carbon steel
-
Magnesium
-
Nickel
-
Titanium
-
Zinc
- Personal account manager
- Quality assurance
- Payment terms for companies
- On-time delivery by Fractory
Equipment
The main components of electron beam welding equipment are the following:
Electron Gun
The main components of an electric gun are the cathode, anode, grid cup and focusing unit. There are two types of electron guns. Self-accelerated electrons are accelerated using the potential difference between the cathode and the anode. Work-accelerated electrons are accelerated using the potential difference between the cathode and the workpiece.
Power Supply
DC power is used in the electron beam welding method with 5-30 volts for small equipment and 70-150 volts for large equipment.
Vacuum Chamber
The pressure for partial vacuum is at 10-2 to 10-3 mbar, while hard vacuum uses a range of 10-4 to 10-5 mbar.
Applications
The diversity of EB welding allows the ability to weld metals with varying thicknesses, making it a flexible option for welding complex parts such as transmission assemblies or small electronic components. It’s also a great option for welding metals with different melting points and thermal conductivities.
As electron beam welding technology is highly automated and delivers a clean result with repeatable accuracy and minimal distortion, there is no need for post-weld machining. Some of the industries benefitting from this include aerospace, automotive, medical, nuclear, oil and gas.
Electron Beam Welding vs Laser Welding
While the basic principle of electron beam welding and laser welding is similar on the surface, there are some distinct differences that make each of them unique:
Heat source
EBW uses a focused beam of electrons, while the laser welding process uses photons to generate heat.
Vacuum environment
Both processes can be performed in a vacuum environment, protecting the weld pool from contamination against air molecules and improving the weld quality. Conventional laser welding is done under atmospheric conditions with the help of inert gas shielding or a combination of gases.
Welding speed
Laser beams require high welding speeds since it vaporises the base materials, creating fumes. The electron beam welding process can accommodate different welding speeds while still achieving deep welds.
Power consumption
Electron beam welding converts around 85% of the electrical input into usable power. In comparison, laser welding only converts up to 40% of electricity to usable power, even with the use of modern tools.
Advantages of Electron Beam Welding
-
Can reproduce precise welds at rapid weld speeds.
-
A narrow heat-affected zone allows for welding delicate assemblies.
-
Clean welds since EBW is done in a vacuum environment.
-
Ability to join dissimilar metals.
-
High weld penetration range.
-
Most penetration depths don’t require filler material.
Disadvantages of Electron Beam Welding
-
High initial costs.
-
EBW machinery requires frequent maintenance to function correctly.
-
The process requires highly skilled machine operators.
-
The size of the vacuum chamber limits weld size for traditional EBW.
-
Extreme precaution is required from radiation.