MIG and TIG welding both use an electric arc and shielding gas to join different metals. While they are quite similar on the surface, each has its own distinctive features.
When welding methods were inadequate to join aluminium and magnesium alloys in the 1940s, metal inert gas (MIG) and tungsten inert gas (TIG) welding became a breakthrough solution. This success gave rise to its popularity across different industries to this day.
TIG is less aggressive and the use of filler material is optional, making it better for use on thin metals. MIG allows for better penetration on thicker materials from the combination of its shielding gas, power source and process.
Let’s take a closer look at how two of the most common welding methods set each other apart.
- MIG welding is faster and easier to learn, boasts high production rates and is ideal for thicker materials.
- TIG welding offers higher precision and control, better for thin materials.
- TIG welding generally produces cleaner, more aesthetically pleasing welds, making it suitable for projects requiring a refined finish, while MIG welds are often slightly less visually appealing.
- MIG welding process uses a continuously fed consumable wire electrode, while TIG uses a non-consumable tungsten electrode with a separate filler metal.
MIG and TIG Welding Process Comparison
MIG welding or gas metal arc welding (GMAW) uses a consumable electrode to weld two pieces of metal. TIG welding or gas tungsten arc welding (GTAW) is a type of electric welding that uses a non-consumable electrode to join workpieces. Both use electrical current to heat the weld area until it forms a molten metal joint.
While MIG and TIG welding share a similar process, there are some key differences that make each unique.
These subtle details have a major impact on the output of the weld when summed up.
Electrode
The most observable difference between MIG and TIG welding is in its use of an electrode. MIG welding process uses a continuously fed consumable wire electrode to join two pieces of metal. TIG uses a non-consumable tungsten electrode with a separate filler metal.
While you can perform MIG welding using only one hand, TIG welding requires you to have your TIG torch in one hand and the filler material in the other.
The hand-held filler rod is sometimes a nuisance for welders, but it offers greater control since you can precisely apply the filler material along the electric arc.
Shielding Gas
TIG welding mostly uses pure argon or a blend with another non-reactive shielding gas, such as helium or nitrogen, in order to avoid contamination.
MIG welders commonly use a blend of argon and carbon dioxide as it offers more penetration, which is better suited for thick materials.
Another key difference between MIG and TIG welding is the rate at which it is expelled on the torch. A MIG welder typically runs its gas at 35 to 50 cubic feet per hour, while a TIG welding gun requires a gas flow at 15 to 25 cubic feet per hour.
Welding Torch
The torch is a key component that contains the electrode and shielding gas. For MIG torches, the electrode is consumable, while TIG welders use a non-consumable electrode with the option of feeding a separate filler material.
While MIG and TIG welding equipment can both use water and air-cooled torches, water-cooled torch is preferred for a TIG welder due to its potential higher temperatures.
Power Source
A MIG welder uses a DC power source to create stability in the electric arc as well as to give enough penetration of the metals.
TIG welders offer versatility to AC and DC power sources. The selection will vary depending on the metals to weld, the desired electric arc, and the amount of spatter in the weld pool.
- Personal account manager
- Quality assurance
- Payment terms for companies
- On-time delivery by Fractory
Different Materials – Which Method to Prefer?
The use of MIG and TIG processes varies depending on the situation. In order to find what suits your project best, it is important to identify the materials involved. Although most metals can be welded using both MIG and TIG welding, there are some instances where one stands out.
Stainless Steel
Since this metal is composed of alloys that are low in conductivity, it keeps heat for longer periods of time. Arc welding stainless steel requires precision to avoid excess melting.
TIG welding is perfect since it can create narrow beads in the weld pool, avoiding critical areas of the metal. However, some mass productions may benefit from MIG welding.
Mild Steel and Cast Iron
MIG welding is a popular choice for welding mild steel and cast iron because it is easy to use, produces strong welds and offers high deposition rates. A MIG weld doesn’t necessarily offer beautiful welds, but often it doesn’t matter since these metals often go through different surface coating procedures.
Aluminium
It is important to minimise the contact of bare aluminium with air as it can react to form aluminium oxide. TIG welding can form precise beads from the welding torch is optimal for cutting through the layer. Running it in AC will also result in cleaning the aluminium oxide on the surface.
Other metals like copper and titanium can be welded using both processes but TIG is generally preferred for welding thinner aluminium stock to guarantee clean welds with no spatter.
MIG vs TIG – Pros and Cons of Each
Before you decide which welding technique to choose, take a look at the pros and cons of using TIG and MIG welding for your project. Knowing this information will not only help you decide which one to use, but it will make you a better welder overall.
TIG Welding
Pros
-
TIG welds are higher in quality.
-
Filler material is optional.
-
Foot pedal offers greater precision.
-
TIG offers versatility to a wide selection of materials.
Cons
-
You need a clean metal surface before welding.
-
It is a slow welding process.
-
It requires skill and experience to achieve high-quality welds.
-
A TIG welder is more expensive with added maintenance costs.
MIG Welding
Pros
-
Faster weld time.
-
Welding equipment is cheaper, and its materials are readily available.
-
Easier to create a strong weld.
-
You can weld at difficult angles.
Cons
-
MIG welds are not as strong as TIG welds.
-
Harder to control the weld bead.
-
Inability to weld thin metals.
-
Requires protection from fumes.
TIG and MIG Welding Applications
Thickness
MIG welding is usually the best choice when dealing with thicker metals as it has high penetration along with the feed wire supplied into the weld puddle. It is mostly used in manufacturing pressure vessels and in the construction industry.
TIG welding is preferred for thin materials that are delicate and prone to defects. Its applications include pipe joints, aerospace and automotive fabrication.
Run Time
The TIG process is usually short, as it is best suited for technical projects. For longer runs, specifically in production, the MIG process is often the choice. The latter is preferred for less complexity and lower overall costs.
Aesthetics
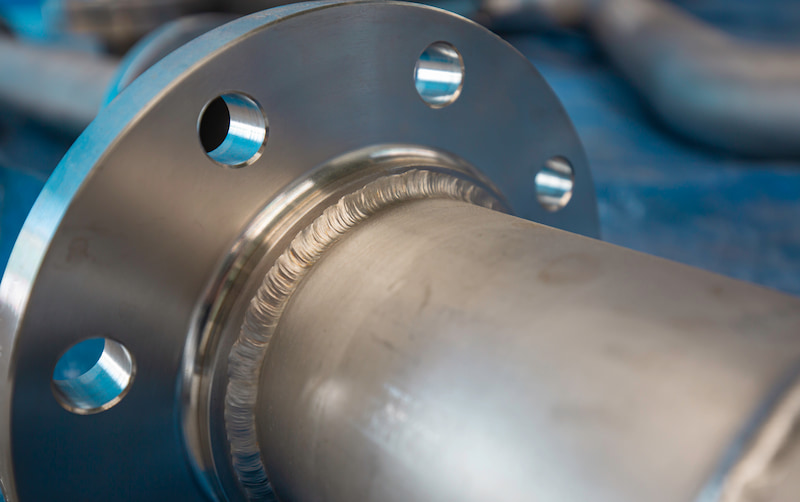
TIG welders are more suited for projects that require control of their heat input. It is easier to achieve consistent beads in the weld pool using this welding technique. This is perfect for artwork, projects, and car repairs.
We often use MIG welding for fast welding when aesthetic finishes aren’t prioritised. MIG is also chosen if the metals undergo coating or post-processing.
Angle / Reach
A TIG welder is controlled through its foot pedal, suiting it best for easy-to-reach angles and sectors. This is most applicable in bench or shop work, where the material is at a comfortable angle.
MIG welders are preferred when welding at awkward angles since you have a free hand to hold and control the materials that need welding.
Environment
Since both TIG and MIG welding use shielding gas, it is desired to weld in a controlled environment, preferably indoors or in areas with little wind.
In conditions where it is unavoidable, you can opt to use flux-cored welding wires. The flux reacts with the arc to form a shielding gas that protects the weld. You need to adjust some machine parameters for this to work and consider the slag it leaves behind.
Experienced Welders
MIG welding is easier to learn because of its straightforward process. A beginner can easily make good beads on a project. TIG welding requires higher skill and experience as it offers more versatility in welding.
Being knowledgeable in both gives you the edge in choosing the right welding process when doing different projects.
Automation
Technological advancements allow robots to produce MIG and TIG welds in manufacturing and assembly. Compared to manual welding, robots can repeatedly produce consistent, precise welds at a rapid rate.
Conclusion
Welders often debate the merits of MIG vs TIG welding. Both have their pros and cons, but neither can be seen as definitively “better” than the other.
We often generalise MIG welding as faster and easier to learn, while TIG welding produces a higher quality weld. However, both of these statements can have exceptions, and the choice really depends on the project you’re working on.
Several factors should always be considered when doing a specific welding project: type of material, quantity, cost, equipment, post-processing needs, etc.
As of today, both welding processes are popular and widely used. We can anticipate the creative advancements that will come forth in the coming decades.