Powder coating is one of the most common ways of surface treatment in the metal fabrication industry. It gives the part or product a nice aesthetic finish that also protects it from all sorts of material wear.
We will cover the basics of powder coating, including how it works and coating parameters to choose from.
This will also come in handy when using our online manufacturing platform, where you can choose the colour and finish for your products and it will be calculated into the production quote along with cutting, bending and whatever else is necessary for the whole fabrication process.
How Does Powder Coating Work?
Powder coating uses a powder made out of polyester and pigments which is stored in a pressurised gun’s hopper. An operator hitting the trigger releases a flow of air that takes the polyester particles along with it.
The particles get positively charged inside the gun’s “barrel” by an electromagnetic coil. At the same time, the coated part is grounded and has a negative charge.
As a result, the powder that gets sprayed onto the workpiece will stick to it. Also, the magnetic force manages to pretty much level it, leaving a nice smooth powder coat and negating any problems with patches.
Once the coating is set, the part will go into the oven. At about 200° C, the powder melts. In a matter of 10 to 20 minutes, the curing process turns the molecular structure of the powder into a resistant and elastic coating.
The elasticity is one of the reasons that makes powder coating such a durable surface treatment service to protect your metal products from the environment.
Gloss Level
There are three things to consider when choosing your powder coating properties – colour, gloss level and texture.
Colour is pretty self-explanatory, so we will move on from that. As a side note, there is also an abundance of colours to choose from on our platform with RAL codes for specifying the exact needs.
It is important to highlight that the standards for gloss levels in use are not uniform across all service providers. There is always a gloss level in numerical form next to the description that may vary quite a lot between different suppliers. So we would advise to always look at that number rather than the description.
For example, matte can be anything below 10 for some, up to 30 with other surface treatment service providers.
For this guide, we have included one of the most widespread classifications of gloss levels which is also in use here, at Fractory.
Matte
Matte, also known as flat, has a gloss level of around 30 (+/- 5%). While it does reflect some of the light, the reflection is faded and not clear-cut.
Suitable for hiding surface imperfections. It is important to note that a matte finish is harder to clean compared to higher gloss levels because of the surface flatness levels.
Gloss
This is the most common gloss level that stands around 70 (+/- 5%). It is easier to clean that a matte finish and provides less surface friction.
The gloss finish leaves a nice reflection that is not very highly defined.
High gloss
Levels above 80 (+/- 5%). Very shiny and reflective. A high gloss also brings out any surface imperfections, so the metal surface itself should be very even and well finished to reach a great result.
Also, the smooth surface is perfect for cleaning which can play a big role in industries like medical and food processing.
- Personal account manager
- Quality assurance
- Payment terms for companies
- On-time delivery by Fractory
Texture
Texture is another feature that can be modified as per the requirements. Usually, powder coating needs subject only colour and gloss levels because texture also restricts the available range of the latter.
The textures are all great for hiding surface imperfections, as they are quite rough and therefore the smoothness of the surface is not a big factor in the final outcome.
With most service providers, there are three classifications to choose from.
Sand texture
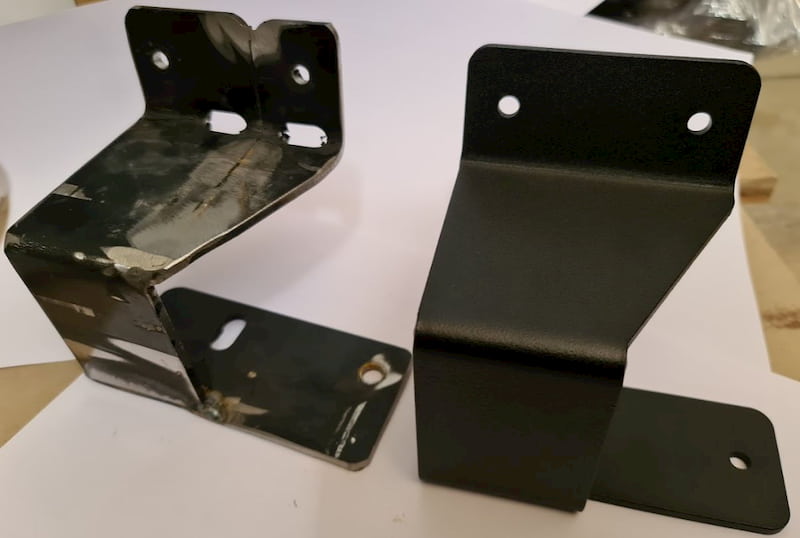
The sand texture gets its name from the surface being pretty similar to sandpaper. It also limits the gloss levels to 20.
The rough surface increases friction, so it can come in handy as a property required in certain applications.
Wrinkle texture
The wrinkle texture is similar to sand texture. However, the difference is in the roughness. Wrinkled texture provides an even better grip because of higher surface roughness.
Hammered texture
The hammered texture is similar to the surface of a golf ball or an orange peel. It has higher gloss levels than sand or wrinkle.
The texture adds durability and does not need much surface preparation.
Powder Coating vs Wet Paint
Wet painting is the traditional way of applying a coloured coating to a part. Using a spray, pump or other pressurised vessels, the wet paint is delivered evenly onto the surface to dry.
So let’s compare the perks and drawbacks of both processes to get a better overview of the options as they are alternatives to each other.
Wet paint benefits
As said, powder coating needs heating of the part in order to solidify the coating. But not all parts are suitable for heating, so wet paint comes in handy whenever there are limitations like that.
It also provides a larger variety of different colours.
Wet paint is also suitable for a much thinner layer than a powder coat, making sure that less paint is used to reach the desired outcome.
Wet paint disadvantages
The main drawback is definitely that wet paint is just not as durable as powder coating. It may require maintenance and even adding another layer at a later point to keep the nice look.
Another thing to keep in mind is the necessity for multiple layers of coating. The wet paint may start flowing and getting the desired result may be somewhat more difficult to achieve.
Powder coating advantages
Powder coating leaves a thicker finish that lasts for a long time to protect the metal from the environment.
Secondly, the process itself is pretty easy and straightforward. As the coating is thick, there is no need for any pre-treatment. Only one layer can leave a high-quality finish to your products.
Powder coating services are also a more environmentally safe alternative because it uses less organic compounds.
Lastly, the surface finish is very even. While spray painting may start to flow, powder coated finishing does not depend on the position of the part. Whether it is vertical or horizontal, the paint will not start flowing.
Powder coating disadvantages
There are two main drawbacks when it comes to powder coating.
Firstly, the coating is thick. Although we also brought it out as an advantage, it may not always be sought after. A thin finish with powder coating needs expert skills because otherwise the surface may leave a bumpy layer because of the polymer thinning process.
Secondly, it may be costlier for small-batch jobs. The whole process takes longer and requires more costly machinery and thus, it may not be the best choice when looking to produce only a few items at a time.
Choosing a Surface Finish
On our online metal fabrication platform, you can choose any RAL colour along with a gloss level.
These 2 are the main parameters for most cases when looking for powder coating services. Gloss is the default option as it is the most common option for engineers to use.
Applying the high gloss level needs more surface preparation that can result in a higher price. Otherwise, even grind marks and other scratches can be visible to the naked eye.
However, as already mentioned, some industries and use-cases do need to either leave an eye-pleasing aesthetical look or have a more practical purpose in the form of easier surface cleaning.
In this case, we would suggest choosing higher gloss levels for powder coating to reach the intended objective.