Faultless engineering exists only in theory. Everybody makes mistakes that even WD-40 cannot solve. Our engineers still tried to compile a comprehensive list to keep in mind when designing, to minimise the amount of those problems.
Make Sure What the Requirements Are
Write them down and keep them in front of you at all times during the designing process. Cross out the demands that have been met and add new ones, if necessary. Keep it up to date.
Generate at Least 3 Solutions
First, go through the concept generation process to draw up a lot of different ideas. Then settle on at least 3 solutions that could actually work.
If you are having a hard time at coming up with good solutions, take a look at this list of best websites for mechanical engineers. Many of them include great ideas that may aid you on the journey to a good design.
Build Your CAD Files Logically
This an important engineering tip. Use as few features as possible to build your parts. A shaft can be done using one command and a sketch (revolve) or multiple protrusions, followed by chamfers and radii. If your CAD program has a shaft feature (Inventor does), then use it. Your colleague will appreciate your considerate nature, if she has to redesign your part at a later time.
Design for Price
You may design the most beautiful machine ever but nobody will buy it, if the price is double of your competitor’s, unless the machine is a car. Check the prices of different solutions to compare and make choices accordingly.
Design for Beauty
If the customer is paying €40,000 for your machine or construction, he won’t want to get something that looks straight from the landfill. Looking good might be the edge in a competitive market. Turn to a laser or plasma cutting service to give smooth edges and trim down some unnecessary weight, in style.
Make It Modular
You might need to make another similar product. Look ahead to avoid cursing at a later time. Modular design will give you the option of only updating a part of the assembly, leaving most of it untouched. It also gives you the possibility to have more standard parts in stock, diminishing your delivery times.
- Personal account manager
- Quality assurance
- Payment terms for companies
- On-time delivery by Fractory
Identify the Parts That Shall Get Worn Most Often
Make them easily accessible and replaceable.
Make Sure Everything Can Be Assembled
The bolts may look nice sitting there fastened in your virtual assembly but can someone reach it with a spanner? Or can a rivet gun be used in that tight space? A very common mistake that can be easily avoided.
Avoid Over-Dimensioning
Nobody wants to pay for unnecessary weight. Use Finite Element Analysis software to analyse the strength of the structure. Check those calculations manually. Optimise your design accordingly and choose the right type of metal for your application.
A highly advanced way to tackle this point is by using CAD software with possibilities for creating models through generative design. This feature allows to minimise the use of material but also sets its own limits to the manufacturing technologies suitable for producing the part.
Keep the Thinking in the Drawing Room
The positioning of the parts in a weld-assembly can be one-way only, if notches and holes are used. Only general dimensions are needed then, keeping the drawings easy to read. Nobody should have to ask for help when looking at the drawings.
Stop Wasting Time on Detailed Drawings
When using laser cutting or plasma cutting, no dimensions are needed for part drawings. Do not waste time on something that is unnecessary (your dimensions will have to be deleted anyway). You can also get instant laser cutting quotes now based on 3D CAD models.
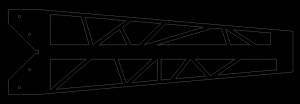
Check for Interferences
This function can usually be found under the Inspect tab. Try it out and modify the inputs according to needs. The easiest way to recognise blunders that would otherwise need cutting or redesigning.
Use the Appropriate Constraints
Leave the assembly with the degrees of freedom it actually has. Then start moving and playing around with it. You may be surprised by what you managed to leave unnoticed before.
Go Back to the First Step
Take a hard look at your design. Are all the requirements met? Small tweaks may have affected the whole more than you thought at the time. Now let your imagination flow once more. Can it take -30 degrees or a metre-thick layer of snow during winter? Can it survive a collision with a disoriented forklift? What if the average flow of material is 1000 kg/hour but the conveyor is loaded with 1000 kg in the first 20 minutes, followed by silence in the next 40 minutes?
Those questions should be asked in the beginning but must be asked before the customer. Choosing materials with suitable mechanical properties is essential.
Remember the Manufacturing Process
You can make pretty much anything in your CAD to suit the needs. In reality, it may be difficult or even impossible to manufacture the parts. Always design your details keeping the manufacturing process in mind.
Make you life easier with sheet metal fabrication services online!