Sheet metal is the basis of all engineering today. We can see it everywhere – from cars and machinery to house facades and furniture.
To utilise sheet metal to its full extent, engineers should first know a thing or two about it. This includes standard measurements, materials, differences in manufacturing and possible forming methods.
What Is Sheet Metal?
Sheet metal is one of the shapes and forms metal can be bought in. Sheet metal is any metal that has a thickness in between 0.5…6 millimetres.
There are other measurement units used to categorise metals by thickness, though.
Millimetres, Mils & Gauge
Foils, sheets and plates are pretty much the same, with the only difference being in thickness. Thickness is measured in 3 ways – millimetres, mils and gauges. While millimetre is a pretty straightforward unit, mils and gauges are only common in engineering and manufacturing.
One mil equals to a thousandth of an inch. As the British often use “mils” as a plural for millimetres, it can be a little confusing but the difference is important.
Gauge is another unit for measuring sheet metal thickness. Although official standards discourage the use of gauges, they are not all that rare. Gauge represents the thickness of a metal in relation to its weight per square foot. A higher gauge number means a smaller thickness.
As it is related to the weight of a metal, the actual thickness (mm) for the same gauge, is different for various metals (e.g. 12 mm steel vs 12 mm aluminium).
Foil, Sheet and Plate
Having gone over the primary measurement systems, we can now look at the categorisation of foils, sheets and plates. For our purpose, we are going to stick with millimetres as the unit of measurement.
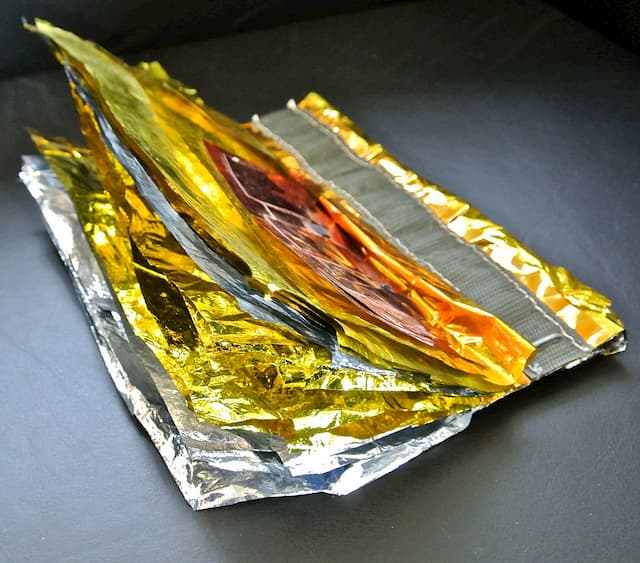
Metal foil is especially common with aluminium, often referred to as tinfoil. The thickness of foil is usually up to 0.2 mm.
Sheet metal is the next in line. The thickness of sheet metal starts from 0.5 mm and goes up to 6 mm. Anything above that is a metal plate.
The thin sheet metal is easy to form, while still providing great strength. At a relatively cheap price, it makes a great fit for most engineering purposes. That is why we see it everywhere around us.
At the end of the article, we will be discussing different forming methods used with sheet metal.
Common Materials
Pretty much all the common engineering metals are also used in the form of sheets. Some of them are carbon steel, stainless steel, copper and aluminium. Choosing the right one for you comes down to the application and requirements of your product.
Metal sheets have the same mechanical properties as the base metal. Thus, steel sheets have high tensile strength and durability suitable for use in constructions and machinery.
At the same time, copper sheets often find use as a decorative layer on modern buildings.
Standard Sizes
Standard measurements apply to both sheet sizes and thicknesses. While achieving large sheet sizes have a few workarounds through welding, you cannot really look past the thickness tables.
Standard Sheet Metal Measurements
Knowing standard sheet sizes helps you with optimising your part layouts. Many times have we received parts for production that are just a bit larger than the standard size. That means more scrap and higher overall costs for the customer.
Also, another thing to bear in mind here is the availability of different sheet sizes. While small, medium and large sheets are pretty much always in stock at every sheet metal fabricator’s warehouse, oversized sheets may not be.
Many of them may also not have the machinery to cut such large sheets. So knowing your manufacturers’ capabilities comes in handy here.
Sometimes you can just weld together two smaller sheets but it is not the optimal solution. Especially when putting high emphasis on the aesthetics of your project.
Standard Sheet Metal Thickness
The table above shows standard thicknesses for both sheet metal and metal plates. As you can see, each type of metal has its own standards.
Also, it is good to not only pay attention to the starting and ending points but the actual values. Someone asking for non-standard thicknesses is quite frequent.
Exceptions to this table definitely exist. We would just advise you to follow these thicknesses because of the difficulty of finding the materials. All of the ones above are readily available with many sheet metal fabricators.
- Personal account manager
- Quality assurance
- Payment terms for companies
- On-time delivery by Fractory
Hot-Rolled vs Cold-Rolled Sheet Metal
There are two ways of producing sheet metal – hot rolling and cold rolling. Looking at the standard thickness table above, you can see how those two are used. In the case of construction steels, cold rolling only goes up to 3 mm. From there on, the sheets and plates are hot rolled for cost-efficiency purposes.
Although the hot rolling process again starts from 3 mm for stainless steels, cold rolling covers all the sheets, i.e. up to 6 mm.
For engineering purposes, it is important to differentiate the two. For precision applications, cold rolled steels are preferred as we have more control over the final dimensions. This is because in hot rolled steels, after cooling, the steel shrinks slightly and the shape might change a little.
Forming Processes for Sheet Metal
So we finally made it to the forming methods for sheet metal. There is a plethora of options on the table and the decision rests on you.
The choice mostly depends on the required outcome. But many of those methods get you a seemingly similar or matching result. Then it comes down to cost (often depending on batch sizes), availability and desired accuracy.
Sheet Metal Bending
Bending is a forming process in which sheet metal is bent into the desired shape by applying bending stress. The sheet metal is bent so plastic deformation is reached. That prevents the metal from regaining its former shape.
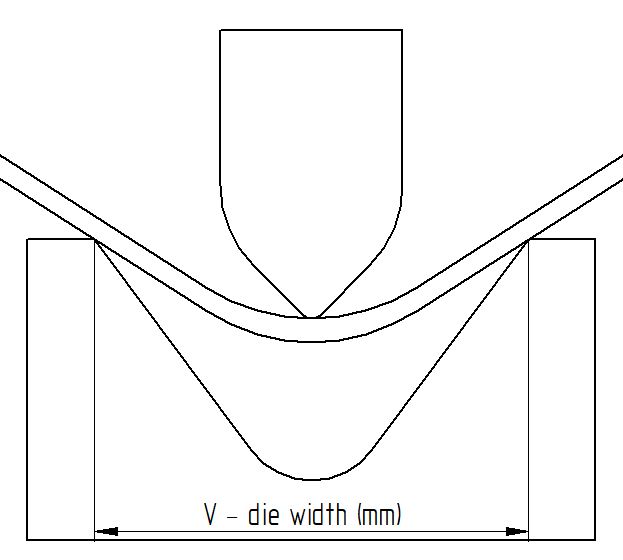
Parts such as flanges and corrugations are created by bending. The most common form of bending is V-bending. There, a V-shaped die and a punch press together to give the sheet the desired form.
Edge bending is another common method to bend flanges using a wiping die and a punch.
Sheet Metal Curling
Curling is the process of forming a circular ring at the edge of the metal sheet to make it safer for handling.
There is a difference between a curled edge and a tear-shaped hem. In curling, the initial edge is rolled into the formed circle whereas, in the tear-shaped hem, the initial edge is still exposed.
Curling can also be classified into an off-centre and an on-centre roll. Off-centre rolls have the centre above the level of the sheet, whereas on-centre rolls have the centre at the same level as that of the metal sheet.
Sheet Metal Decambering
Decambering is the process of removing camber from a sheet of metal. In a sheet of metal, especially in strip-shaped parts, a horizontal bend is produced when it is flattened into sheets.
In decambering, we remove this horizontal bend by flattening the edges to remove the camber. The force is applied on a deformed edge, and not on the face, to push it into a straight form. It is usually carried out on limited length sections.
Deep Drawing
Deep drawing is a sheet metal forming process in which a sheet’s shape is changed to the desired shape in multiple stages using a series of dies. Only if the depth of the shape formed exceeds the original diameter of the sheet, it is considered deep drawing.
Punches and dies are used to create changes at every stage. Using this process, a sheet is converted into many different shapes like a fuel tank, sink, and automobile parts. Deep drawing is mostly used for large-batch production.
Sheet Metal Expanding
In this metal-forming process, a sheet of metal is passed through perforating scissors where it is cut and stretched into a pattern. Usually, a diamond-shaped mesh is preferred as it has a structural advantage over other shapes.
This forming process is commonly used for manufacturing fences, catwalks, platforms, grating, etc. The process gives a self-draining, strong product that can support the weight it is designed for.
These products can be used where a passage of air or a liquid is needed but there is a need to prevent larger particles from passing, e.g. sifting. The strength of the original metal is retained.
Hydroforming
Hydroforming is an innovative way of shaping metal sheets into the desired shape. In this process, the metal is placed on a die, but instead of a punch, high-pressure fluid is used to shape the sheet.
With this process, more complex parts can be created in a shorter time frame. It is also comparatively cheaper and requires less work. Hydroforming is also compatible with almost all materials such as stainless steel, aluminium, carbon steel, brass, and precious metals.
Since matching dies are generally not needed, hydroforming can be used to form unconventional shapes.
Incremental Sheet Forming
Incremental sheet forming is a metalworking process that gives sheet metal a certain, desired shape. This forming method is only viable with low volumes.
Changes can be made to the product quickly and without much hassle. In this process, the product is formed in incremental steps.
The sheet material is shaped using a single-point sphere.
While the process gives similar results to deep drawing, it does not need a separate set of punches and dies. So the largest advantage of this method is its flexibility.
Ironing
Ironing process is used when the thickness needs to be reduced in a certain area of the sheet metal. This enables the manufacturer to get a uniform wall thickness when deep drawing products.
A good example of ironing is the process of manufacturing soda cans. The walls of the can need to be thinned to a predetermined thickness. Usually, 2 or 3 ironing processes with different dies are needed to create the desired thickness in aluminium soda cans. This ironing process is carried out in combination with deep drawing.
Laser Cutting
Laser cutting is being used more and more for sheet metal cutting applications. It is precise and the finish is extremely smooth. CNC machines are generally used to cut specific shapes.
After feeding the program, the specific cut is carried out by laser. Laser cutting has the advantage of flexibility. When needed, changes in the required shape can be carried out easily. It is also possible to cut metal sheets into extremely complex pieces using laser cutting services.
Photochemical Machining
Photochemical machining is a process in which controlled corrosion is carried out to create sheet metal parts as per requirements.
In this process, a photoresist and an etchant are used to give the metal sheet its shape. The method was developed in the 60s and even today is a comparatively inexpensive method.
Photochemical machining can be used to cut any metal. The process is ideal for mass production. If changes are required, they can be easily brought about.
Just like laser cutting, the process is extremely precise and can offer a smooth finish. This process is used to make extremely fine meshes, apertures, flexible heating elements, metal gaskets, electrical contacts and jewellery.
Punching
Punching is a very common technique for cutting holes in sheet metal. The setup consists of a punch and a punching die. There is a very small clearance between the two.
When the punch and the die meet, the material is pressed between the two and with subsequent pushing the shearing force cuts a hole in the sheet. The process is relatively inexpensive in large quantities and capable of punching a hole in strip as well as sheet metal.
Holes of varying sizes can be punched but it is usually recommended that the diameter of the hole required is greater than the thickness of the material being punched. For especially sturdy alloys, the difference between the hole diameter and the thickness needs to be greater.
Rolling
Rolling may be carried out on sheet metals to decrease the overall thickness of the metal sheet or to make it more uniform. In this process, the sheet metal is passed through a set of rolls.
Depending on the temperature the process is classified as hot rolling or cold rolling. In hot rolling, the temperature is around 1400 degrees Fahrenheit for steel. This can help achieve a thickness from 1/16th of an inch to 5/16th of an inch.
In cold rolling, the process is carried out at room temperature. The material is washed with acid and heat treated to achieve a good finish.
Rolling is also another way to achieve large-radii bends. Instead of using press brakes for step-bending, this gives a large uniform radius without the need for continuous manual work in the process.
Press Brake Forming
In this process, a long sheet of metal is bent around a straight axis going through the material. A ‘V’, ‘U’, or a channel-shaped material may be formed depending on the punch and the die.
Although it looks simple, precision bending is a difficult task to achieve in press brake forming. Material properties need to be considered along with the press and the tooling to perfect the amount of springback.
Press brake forming may also be used for smaller parts making it suitable for smaller pieces along with large pieces. Thickness up to 25 mm can be easily bent and the length of the piece can go up to 6 m.
Wheeling
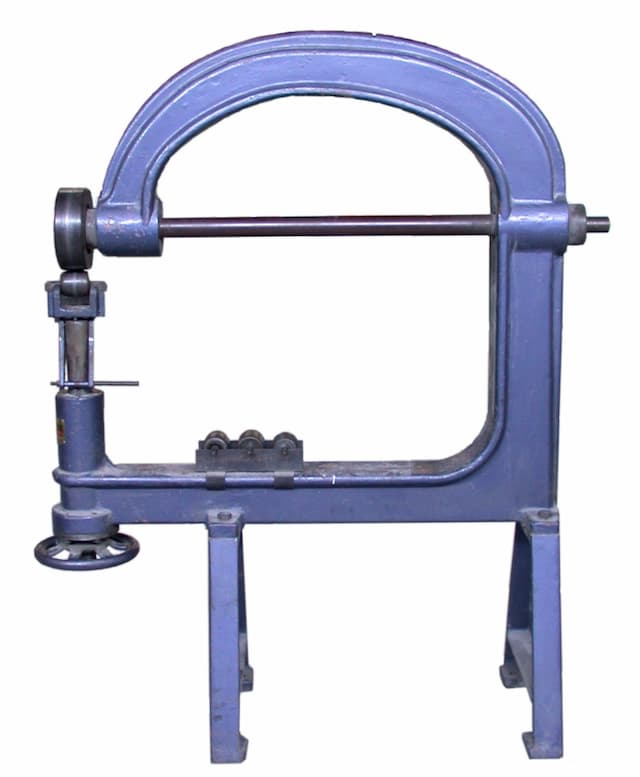
This forming process uses an English wheel to stretch and curve flat metal sheets into required shapes. The method needs highly skilled labour and is therefore expensive. It is not possible to use this method for mass production. Wheeling is mainly used in producing low-volume customised parts for old vehicles.
It is also used for creating sheet metal parts for car prototypes and aircraft.
The shape is produced in stages and at each stage, the operator must compare the formed piece with the reference shape. Different wheels and passing the piece in different directions may be required.
While there is a great variety of metal production services on offer, the importance lies in finding the right fit for your needs while staying cost-effective. All the info above aims to help you do just that.