The image above depicts a drone frame created using generative design. This helps to reduce the weight of the structure by minimising material use while conforming to the engineering inputs.
So, what is generative design?
It is an iterative method for designing new products using the help of CAD software features. These features automatically create a large number of design possibilities when specific data is provided as input. The inputs form the constraints within which the design should perform.
These designs are not invented by AI. They are actually human designs that are refined using artificial intelligence and machine learning.
For example, if we need to create possible designs for a dining table, we need to provide data such as the length, breadth, and height we expect it to be and the load we need it to support.
The generative design program will create a large number of iterations for us which we can fine-tune further as per our preferences. Each iteration can have hundreds of designs within it.
Design Process Using Generative Design
Generative design is gradually transforming the design sector. It helps the designer generate thousands of possible design solutions which would take months to accomplish manually.
There are six common steps to be followed when it comes to creating the perfect design using the various generative design software available in the market today. The six steps are:
Step 1: Problem Definition
In this stage, the project at hand is defined roughly and objectives are laid down. A clear idea of the attributes of the final product is established between the designer and the client by asking questions such as:
- What are we designing?
- What must/must not be present in the final design?
- What are the design parameters and their range?
- What conditions would decide if the project is a success or a failure?
The questionnaire for the design problem must be as exhaustive and the answers as accurate as possible to generate the most relevant design. This step is extremely important for the generative design process as the program will not consider goals that we do not describe when generating models.
Step 2: Data Collection and Entry
Once we have established the problem definition, it is time to move on to collecting the data that the program needs to create our model. This data is collected in at least 2 main phases.
In the first phase, we collect the data needed for model generation and in the second phase, we define the parameters that will be used to evaluate our model.
When it comes to data for model generation, we define both project requirements and as well as constraints. For model evaluation, we define parameters to measure and analyse the model. Defining evaluation data helps the program optimise our solutions. Insufficiently defined data will provide us with many irrelevant solutions besides the relevant ones.
- Personal account manager
- Quality assurance
- Payment terms for companies
- On-time delivery by Fractory
Step 3: Model Generation
Post data entry, we move into the model generation phase. When executed, the program will generate possible solutions that are in line with our defined requirements and constraints.
The generated models are separated into different groups called iterations. Each iteration can contain hundreds of design alternatives.
Step 4: Model Evaluation
Once we have the model ready, the created iterations are checked against initially defined evaluation parameters. The generated designs are also ranked according to how close they are to our requirements.
For example, if we defined the product as a table that has the maximum surface area with the least amount of material, the solution with the maximum surface area will rank higher compared to the ones with less than the maximum surface area. This ranking helps us filter the hundreds of generated designs based on what matters more to us from the defined parameters.
We could select, for example, the cost as our primary filter, and the software would arrange the iterations based on how much they would cost in an increasing/decreasing order.
It is, therefore, recommended to add as many evaluation parameters as possible at the beginning. This may sound counterintuitive as it may limit the number of generated solutions but the generated designs will be much closer to our actual expectations and easier to choose from.
Step 5: Model Evolution
In the model evolution stage, we narrow down our generated design options to filter out non-ideal solutions.
The software sorts through the iterations to choose the most relevant ones and bases new designs on them. The search metrics may have to be customised to find the best design for our needs.
Step 6: Model Selection and Further Refinement
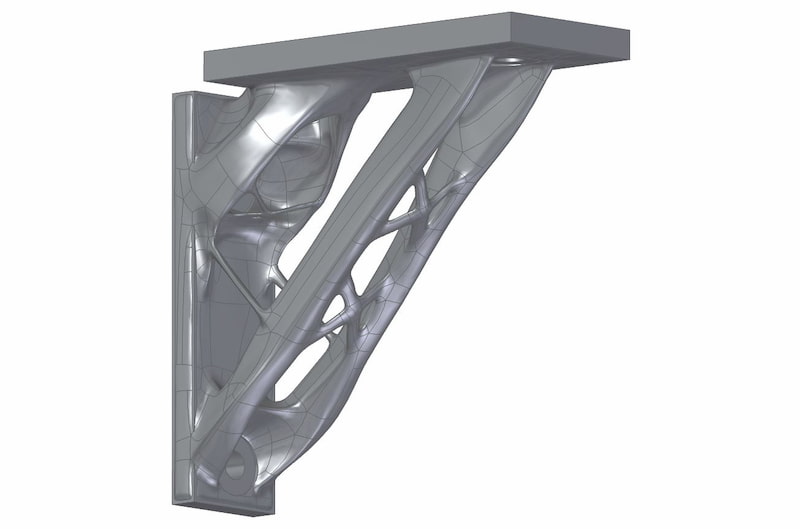
Once we have selected the few designs that are most relevant to us from the design options presented by the software, it is time to further refine them.
Using the same software, the designer makes manual improvements to the top picks. The final design must meet all the predefined criteria and then we can get the client’s approval to complete the design process.
Suitable Manufacturing Methods
While generative design is still not as common as it should be, many popular CAD software have already added this amazing feature.
The iterative designs are usually pretty complex. Still, it is possible to choose the preferred production method during the design phase, so the software will take this into account when generating the possibilities.
So let’s look at the different methods available to create these parts that often come with a multitude of cutouts to optimise the weight.
Casting
Casting is one way to create quite complex shapes as one part, without any welding. So it fits the bill pretty well here.
The cast itself could, for example, be 3D printed depending on the printing as well as the part material. Depending on the casting method used, the cast part may need some post-processing if the surface quality requirements are high.
Also, this method can be paired with machining to arrive at the desirable final design.
Additive Manufacturing
Additive manufacturing usually refers to 3D printing processes. These methods build up the part layer by layer, allowing extreme flexibility for the part design. Which makes it the most appropriate process to select for manufacturing parts created by generative design.
Most printers are able to process plastics but 3D metal printers are a little less common. This is also one of the key reasons why generative design has not picked up in popularity as quickly as some projections said.
Some common additive manufacturing methods are VAT photopolymerisation, material extrusion, binder jetting, sheet lamination, powder fusion, directed energy deposition, and material jetting. You can learn more about them all in our article on rapid prototyping methods.
Injection Moulding
Injection moulding is a great way for large-scale production of plastic parts. The production is quick and achieves a high degree of similarity between parts.
A wide variety of plastic and polymer materials are available for the injection moulding process, and you can use fillers and additives to further increase the strength among other desired properties. A similar approach is also used for metals through metal injection moulding, which combines powder metallurgy with injection technology.
The finishing has high accuracy levels, which means that no post-processing is necessary.
CNC Machining
Precision CNC machining can create very complex parts. 5-axis machining capabilities are flexible and able to twist and turn according to the code instructions.
Both milling and turning can create highly accurate parts and adhere to precise surface finish requirements. The tolerances for CNC machining are famously tight, even when looking at the general ones outlined in the ISO 2768 standard.
Generative Design Software
Generative design is not a CAD application. It is an adjunct to it. As such, the most popular CAD software can incorporate this feature in their existing design solutions to cater to the design industry’s needs. Some of the most common generative design programs are:
Fusion 360 (Autodesk)
This program is a great option for technical design projects. Its salient qualities are its excellent assembly features and parametric design.
The fact that Fusion 360 is free for a year has helped build a huge community of users, making it an extremely well-known software in design, fabrication and manufacturing circles.
The Autodesk generative design feature can be paired with all the above-mentioned manufacturing methods.
Siemens NX
Siemens NX software is a world-class tool that incorporates generative design features. Even though it has a large number of features, the program can be mastered in a short time.
It is a well-integrated product life cycle management software capable of managing the design and creating standard workflows. The cost of use per person is quite high, which limits the use of this software to the enterprise level only.
PTC’s Creo
The Creo generative design architecture by PTC delivers innovative solutions using traditional as well as additive manufacturing methods. Generative design is fully integrated into Creo, so there are no disconnected processes and no need to recreate data.
Creo is an easy-to-use, interactive, parametrically driven program. Creo also harnesses the power of the cloud to simultaneously explore dozens or even hundreds of material and production scenarios, with top options highlighted for the user.
Advantages of Generative Design
Saves Time
One of the most important advantages that a company seeks when mulling over the introduction of new technology is the conservation of time. The amount of time saved directly translates to higher profits as designers/engineers can be freed up to attend to other tasks.
The use of generative design saves a minimum of 20 percent when it comes to project duration. This reduces the time-to-market for new products, which can be the difference between success and failure.
More Creative Options
While designers are known to have excellent imaginations, they are prone to biases. The way they have worked in the past influences their future decisions when it comes to modelling.
Generative design introduces them to new shapes and sizes that they could not have come up with themselves. These shapes and sizes are generally more efficient at accomplishing the product’s intended task, as decision-making is solely based on input data.
Parts Consolidation
An important benefit of this technology is the ability to consolidate parts. A generative design program can create complex parts that can easily replace multiple single parts.
Through additive manufacturing processes, these parts with complex geometry can be manufactured with ease. This ultimately reduces the number of parts in the assembly.
It also simplifies the supply chain and maintenance while reducing the cost of production.
Lightweighting
The weight of parts can be especially important in automotive and aerospace applications, as the total mass of a structure has a significant impact on, for example, the steering of a vehicle and its fuel consumption.
Generative design can be used to reduce weight in places previously neglected to achieve innovative lightweighting. This is an important reason generative design has been adopted eagerly in the aerospace and automobile industries.
Reduces Cost Overruns and Waste
While traditional methods, such as topology optimisation can also reduce cost overruns and waste, they only provide us with one solution.
Generative design, on the other hand, provides us with a long list of possible models, all of which would be within our specified budget with minimal wastage.
Elimination of Weak Design Areas
Compared to traditional methods, it is easier to spot highly stressed or comparatively weak sections in a model with generative design.
Machine learning features enable the software to learn from experience and the design quality improves with time.
Disadvantages of Generative Design
Early in Development
While the concept of automated design is an excellent one, the technology available today is still primitive. Better algorithms need to be written to create more meaningful models that can be used without much manual intervention.
The technology keeps improving over time with new updates constantly bringing in more features and capabilities.
High-Skilled Labour
This design technology can create excellent models for simple objects, but as we move on to more complex parts, extensive knowledge of the software and its backend is required to save time and effort.
The designer must be capable of using ML and AI to their advantage, or the created models may not be as good as they can be. This means more knowledge and experience are necessary to churn out relevant design products in a short amount of time.
Too Many Choices
While this may seem counterintuitive, having a wide variety of choices is not always desirable. An unreasonably large number of choices can easily overwhelm the architect and, in some cases, actually require more time to handle than creating a manual design from scratch.
This problem, though, gets better over time as the program learns how to sort the options, using previous data about the final solution selection.
Fear for Human Jobs
There is an underlying concern among the designers and architectural community that this technology will reduce the number of opportunities for architects and designers.
While this fear is not completely unfounded, the promoters of this technology believe that the designers only need to expand their skill set to adopt this technology. They also hold the firm conviction that the technology will only be a tool in the designer’s toolbox and will not affect the job market.
As a side note, we at Fractory firmly believe that industrial automation is the friend of engineers for creating better designs at lower costs and quicker rates.
High Upfront Costs
Generative design capabilities can be added to existing CAD programs that the company is currently using. Despite this obvious advantage, the technology is still costly when used for commercial purposes.
These programs depend on how many designers will be working on the system at a time, and thus, for large organisations, the initial investment can be quite heavy and a major deterrent to its introduction.
Conclusion
Generative design technology is a culmination of the awesome power of AI, ML, and a designer’s talent. With the advent of high processing power and advanced scripting capabilities, this technology is surpassing its original constraints to give us amazing designs.
The generated products are capable of following every specified requirement and constraint to provide us with truly innovative CAD models perfect for our needs.
Today, there are still only a few industries that can actually benefit from lowering their overall costs. For example, Airbus shaved off 45% (30 kg) of the weight of a single part. The fuel consumption decrease is equivalent to removing 96,000 cars off the road for a year.
The development and spread of generative design have to go hand-in-hand with the availability of additive manufacturing. Although the real potential will be unveiled in the future, we can see the first strides in the right direction.