Cold welding is a solid-state welding process that requires little or no heat to join two or more metal surfaces together. The first scientific evidence of cold welding was recorded in 1724 when two lead balls were joined together by twisting them after being brought into contact. In the 1940s the cold welding process was formally recognised as a general materials phenomenon where two clean metal surfaces pressed together would adhere to contact in a vacuum.
While cold welding took years to be familiarised, it has become an irreplaceable technique for some industries, being a simple yet ingenious process.
- Cold welding is a solid-state process that joins metals without heat, relying on high pressure to create strong metallurgical bonds.
- Cold welding requires meticulous preparation, as the metal surfaces must be clean and free of oxide layers to ensure a strong bond.
- Cold welding is particularly valuable in industries like aerospace and electronics, where avoiding heat distortion is crucial.
- Cold welding is limited to ductile, non-carbon metals, and is less effective on irregular surfaces.
What Is Cold Welding?
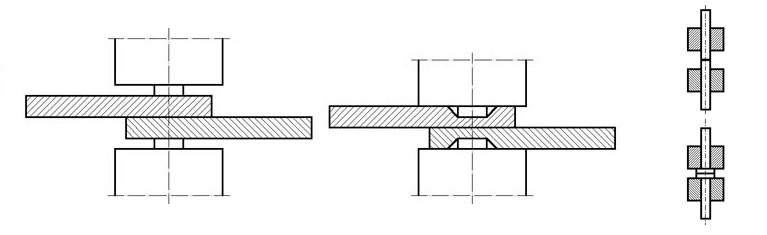
Cold welding, also known as cold pressure welding or contact welding, is a welding process that joins two clean metal surfaces together by using enough pressure to create metallurgical bonds. Unlike other welding processes that use heat and molten material to fuse the metals together, cold welding has the ability to join metals without heat energy to create a near-perfect bond between the materials.
Under normal atmospheric conditions, the metal surface reacts with oxygen creating an oxide layer. This oxide layer acts as a barrier that prevents the atoms from forming a bond. In order to clean the metals for cold welding, the oxide layer is removed through shearing, brushing or using other mechanical and chemical methods.
The metals should be at least somewhat ductile and not have undergone severe hardening. Another limitation of this process is that the metals can not contain any carbon. Cold welding works best when it is conducted in a vacuum, where oxygen is not present.
Some people are unfamiliar with cold welding, as it is an unconventional welding process and differs from the general idea of welding where heat is involved. It is best to understand some so-called cold welding techniques which are actually hot welding processes that either use a conductive electrode or surface.
Cold Metal Transfer
Cold metal transfer is a fusion arc welding process that uses an electric arc to create weld joints. This MIG welding process is mislabelled as cold welding since the heat applied in the weld pool is 90% less than the conventional MIG process.
TIG Cold Welding
The so-called TIG cold welds are achieved by significantly reducing the heat input and precisely applying an electrical arc to a tiny spot just for a fraction of a second. The heat dissipates rapidly, thus this method lacks fusion and is effective only in joining thin sheets of metals.
Cold Welding Process
As a pre-requisite of the cold welding process, the metals are cleaned by removing the oxide layers on the surface by wire brushing or shearing the surfaces. Once the surface contamination is removed, the metals can then be pressed together under high pressure using industrial machines.
This welding procedure works on a microstructural level between the metal atoms, as the electrons will transfer between the two clean surfaces that come into contact. The cold weld bond is strong with few impurities and rough patches but can also be noticeably weaker if contaminants or surface irregularities are present.
Additionally, the time between the preparation process of cleaning the metals and the actual cold welding process is crucial. This time window is short as the atoms on the clean metal surface start to react with the atmosphere. Prolonged exposure may leave an exceptional amount of impurities that will affect the strength of the bond later on. These impurities can be revealed by the use of different non-destructive testing methods.
Only a small number of tools are needed for this relatively straightforward welding method, a wire brush to remove the surface oxide layer and a cold pressure welding machine to allow the freshly exposed metal atmos to come into contact.
Cold Pressure Welding Machine
A typical cold pressure welding machine contains a mechanism for applying pressure (punch press), a punch tool or dies that act as guides for the metals, rollers for the wires or sheets, and a static load to apply the pressure either mechanically or pneumatically.
When cold welding wires, a die with the right size is selected for the wire and is then placed in the cold welding machine. Most of the time, wire cold welding machines are equipped with a guillotine to trim/shear the ends of the metal to remove the oxide layers and achieve flat surfaces.
The two wires or strips are then joined using high pressures. A flash is created in the contact area between the two metal surfaces and the excess metals are removed. Cold welding wires and very thin sheets have been fully utilised in the semiconductor industry, wherein parts are compact and sensitive.
The size of the cold pressure welding machines can differ a lot depending on the type and size of the material. These can range from handheld devices that are mainly used to cold weld copper wires, to machines that are controlled pneumatically.
- Personal account manager
- Quality assurance
- Payment terms for companies
- On-time delivery by Fractory
Metals Suitable for Cold Welding
Metals with similar metallic structures and non-ferrous soft metals work best for cold welding, but joining dissimilar metals is also achievable. Here are some of the most common metals that are often cold welded:
-
Aluminum (including the 2xxx and 7xxx grades which are generally deemed unweldable)
-
Copper
-
Zinc
-
70/30 Brass
-
Nickel
-
Silver alloys
-
Gold
-
Stainless steel
Applications for Cold Welding
Nanoscale cold welding
Ultrathin gold nanowires can be joined within seconds through mechanical contact. The trials have shown great results as the welds have the same crystal orientation and mechanical properties as the rest of the nanowire. Nanoscale cold welding has also been performed between gold & silver and silver alloys, therefore indicating that with further research, the process may be generally applicable.
Aerospace & automotive industry
These industries continuously seek combinations of lightweight and functional materials to improve performance, fuel consumption, etc. This is where cold welding comes in handy, particularly in welding aluminium and stainless steel. This technique allows the materials not to be subjected to excessive amounts of heat, therefore reducing the risk of being too brittle.
Underground wire lines
Cold welding is an exceptional solution in situations where introducing heat to the environment can be hazardous. A well-known example is the safe joining of underground wire lines through cold welding, where heat can be a hazard since it might come into contact with explosive gases.
Manufacturing industry
Heat exchangers used for refrigeration make use of cold welding when making tubular passages in large-sized sheets. Some storage or packaging devices also utilise cold welding when creating butt or lap joints. As an added benefit, joining the metals without heat helps to keep the integrity of the materials.
Advantages of Cold Welding
-
Cold welding produces clean and strong welds. The strength of the created bond is close to the parent metal, if not the same.
-
Cold welding doesn’t create a heat-affected zone (HAZ), which weakens the metal’s structure.
-
Cold welding allows the joining of dissimilar metals such as copper and aluminum alloys.
-
The process is fast with virtually no deformation and warping of the metals.
-
Cold welding work can be carried out in heat-sensitive environments where using other welding processes would not be deemed safe.
Disadvantages of Cold Welding
-
Cold welding requires generous preparation time to clean the metals.
-
Only certain materials can be cold welded. The metals have to be ductile and not have any carbon content in them.
-
Cold welding irregular surfaces is difficult. The process gives the best results when performed on flat surfaces.
-
Joint strength can easily be compromised by contamination. This can be caused by oxide layers, surface irregularities and other unforeseeable reasons.
-
A portion of the material is wasted during preparation (shearing, cutting, brushing)
Accidental Cold Welding
Cold welding gives the best results when the process is performed in a vacuum, meaning that no oxygen is present. This is why there are instances where cold welding has accidentally taken place in spacecraft parts.
The Galileo spacecraft is a great example of an engineering design case wherein the possibility of accidental cold welding wasn’t considered. This nearly hampered the whole operation, costing NASA billions of dollars. On October 9, 1989, Galileo was launched to gather information about Jupiter. When finally reaching the planet after 18 months of space travel, three out of the eighteen specialised antennas, that were supposed to unfurl, had been spontaneously cold welded together.
The parts in the antenna’s mobile structure got cleaned over time due to a lack of oxygen and were fused together when the parts came into contact under high pressure. The relative motion between the surfaces does not exclude the possibility for cold welds to occur. This means that cold welding can simultaneously take place alongside fretting and galling as the metals are subjected to repeated impact and vibrations.
Nowadays, there are countermeasures enforced to prevent accidental cold welding. Some key areas designers and engineers focus on to prevent unwanted fusion are materials selection, lubrication, coating and reduction of the contact surface.
On the other hand, the cold welding phenomenon allows astronauts to effectively perform any necessary repair work outside the spacecraft.
Important Points to Remember
Unlike other welding methods where the metals undergo the liquid or molten phase (arc welding, friction welding, spot welding, etc), cold welding allows to join metals without any heat involved, This process is characterised by uniform and strong results as it does not leave a heat-affected zone in the weld. Although to obtain great results, it is very important to remove the oxide layers and be wary of any surface irregularities. Keep in mind that the process is best performed in a vacuum.
Cold welding helps to solve some of the complex problems that several industries face but it is far from superior, as it has some limitations regarding materials. It can not be performed on metals that contain any form of carbon. This is the primary limiting factor since mild steel is by far the most welded metal.