What is the difference between ferrous and non-ferrous metals?
Ferrous metals (from the Latin ferrum, meaning iron) have iron as their base and make up a large share of the metals in use today. Their popularity stems from properties that make them suitable for a wide range of industries and applications.
Non-ferrous metals, on the other hand, do not contain iron. This distinction is important because it results in a notable change in characteristics, ones not offered by ferrous metals.
Properties of Ferrous Metals
Ferrous metals may include a lot of different alloying elements. Some examples are chromium, nickel, molybdenum, vanadium, and manganese. Those give ferrous steels material properties that make them widely used in engineering.
A list of ferrous metal properties:
- Durable
- Great tensile strength
- Usually magnetic
- A silver-like colour
- Low resistance to corrosion
- Recyclable
- Good conductors of electricity
These qualities make them usable in the construction of long-lasting skyscrapers. On top of that, they are utilised in making tools, vehicle engines, pipelines, containers, automobiles, cutlery, etc.
Ferrous Metals Examples
All of them have different specifications, resulting in a variety of applications. To give a better overview, we made a ferrous metals list:
Non-Alloy Steels
Non-alloy steels are also known as carbon steels because carbon is the alloying element there. Yes, a little confusing as the name suggests one thing, but that’s how it often is in the world of metals. Although there are other elements also present, their content is low enough not to make an impact on the material properties. Those elements are sulphur, phosphorus, silicon and manganese. Sulphur and phosphorus can actually have a detrimental effect on the steel’s quality, but again, not with such low-level content.
Although the term “non-alloy steels” doesn’t get much mention in a typical engineering company as such, our beloved structural steels like S235, S355, etc, belong to this group.
Non-alloy steels are classified by their carbon content as low, medium and high carbon steel. Each has its own uses and the characteristics vary. Also, different treatment methods are available accordingly.
Low Carbon Steel
Low carbon or mild steels contain 0.05…0.25% of carbon. They are pretty low-cost and very well-suited for bending operations. The surface hardness can be increased through carburising.
The low-cost and malleable low-carbon steels are widely used. Some examples include bolts and nuts, forgings, medium-loaded details, etc.
Examples of low carbon steels: C10E/1.1121, C15E/1.1141
Medium Carbon Steel
Medium carbon steels contain 0.25…0.6% of carbon. The higher carbon content increases their strength and hardness compared to low-carbon steels. At the same time, the ductility decreases. The increase of carbon and manganese allows tempering and quenching.
Medium carbon steels are mainly used for making different automotive industry components like gears, axles, and shafts but also bolts, nuts, screws, etc. Steels ranging from 0.4…0.6% are also suitable for everything related to locomotives and rails.
Examples of medium carbon steels: C40E/1.1186, C60E/1.1221
High Carbon Steel
The carbon content numbers for high-carbon steels vary according to different sources. Some have more sub-groups, while others stop with high carbon steels that start with 0.6% carbon content and end around 1%. We’ll go with the second interpretation.
These are the strongest of this group, making them suitable for applications where resistance against mechanical material wear is needed. Another quality of high-carbon steels is their tendency to keep their shape. This is why tool steels have a lot of different applications in the field of engineering.
As a downside, the weldability, ductility and impact toughness are all inferior to steels with less carbon.
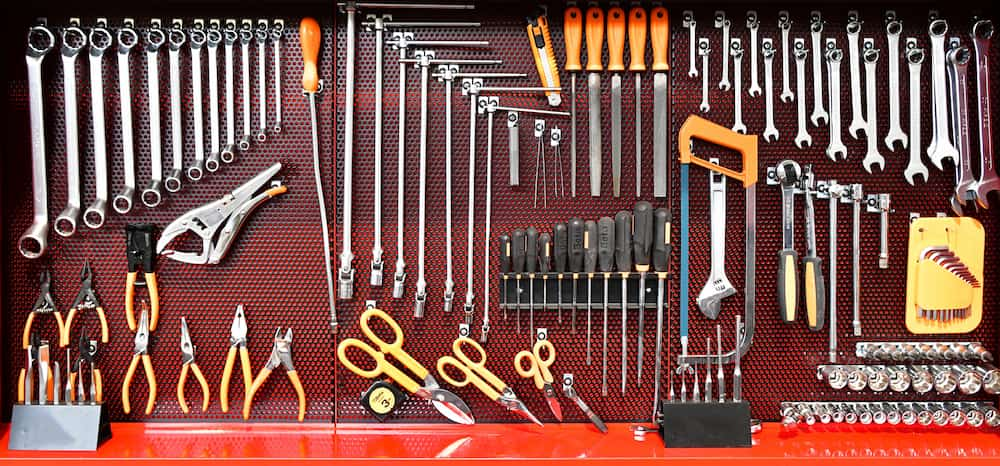
The shape-keeping quality makes them useful as springs. Other use cases include blades, rail steels, wire rope, wear-resistant plates, all kinds of tools, etc.
Examples of high carbon steels: C70U/1.1520, C105U/1.1545
Alloy Steels and the Alloying Elements
Alloy steels make up another subgroup of ferrous metals. Steel’s alloying elements are chrome, nickel, silicon, copper, titanium, etc. Each has its own effect on material properties. Of course, they are usually combined, so the end products have a bit of everything. We discuss how the most common elements affect the outcome.
- Personal account manager
- Quality assurance
- Payment terms for companies
- On-time delivery by Fractory
Chromium
Chromium is the element responsible for creating stainless steel. The presence of chromium at levels above 11% makes a metal corrosion-resistant. As discussed in the material wear article, the protection takes place through creating an oxidised chromium layer on top of the metal. This means that the base metal does not come into contact with oxygen and the danger of corrosion is greatly diminished.
Therefore, it is ready for use without any protective coating. You can achieve a great aesthetic result by choosing the right stainless steel surface finish for your application.
On top of that, chromium also increases tensile strength, hardness, toughness, resistance to wear, etc.
Manganese
Manganese improves ductility, wear resistance and hardenability. The latter is done through quenching, where manganese has a significant impact. It diminishes the danger of defect formation during the process by making it more stable.
It also eliminates the formation of harmful iron sulfides, increasing strength at high temperatures.
Nickel
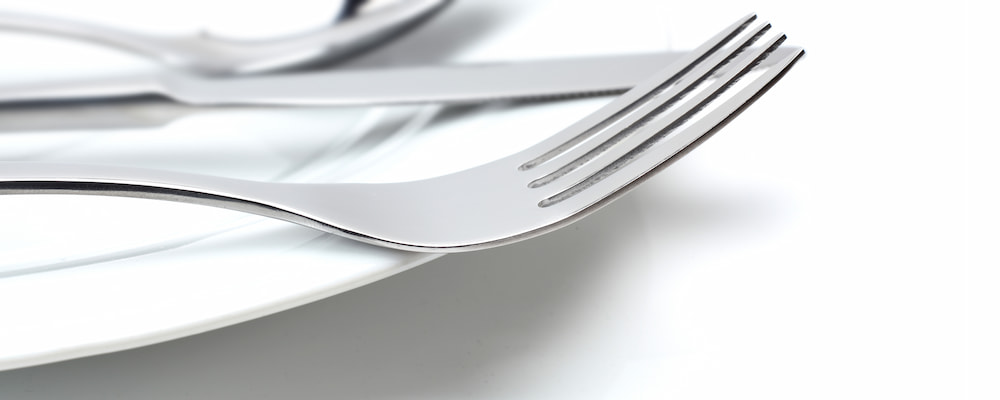
NIckel’s main purpose is to increase ductility and corrosion resistance in combination with other elements, namely chromium. When chromium content is around 18% and nickel at 8%, we get extremely durable stainless steel.
Silicon
Silicon is a metalloid, a category of elements with properties between metals and nonmetals. It enhances strength and provides elasticity, especially in applications like springs. Additionally, silicon significantly increases a metal’s magnetic properties, making it valuable in electrical steels used for transformers and motors.
Titanium
Titanium improves strength and corrosion resistance and, in addition, limits austenite grain size.
Vanadium
The formation of vanadium carbides limits the grain size. This has an effect on increasing a material’s ductility.
It also increases strength, hardness, wear and shock impact resistance. Because of its effectiveness, the amounts must be held low. Otherwise, it can have a negative impact on material properties.
Molybdenum
Molybdenum has a large effect on steel alloys at high temperatures. It improves mechanical properties but also corrosion resistance and acts as an amplifier for the effects of other alloying elements.
Cast Iron
Cast iron is an alloy of iron and carbon, with a carbon content somewhere between 1.5 and 4 percent. There are also other elements present – namely, silicon, manganese, sulphur, and phosphorus.
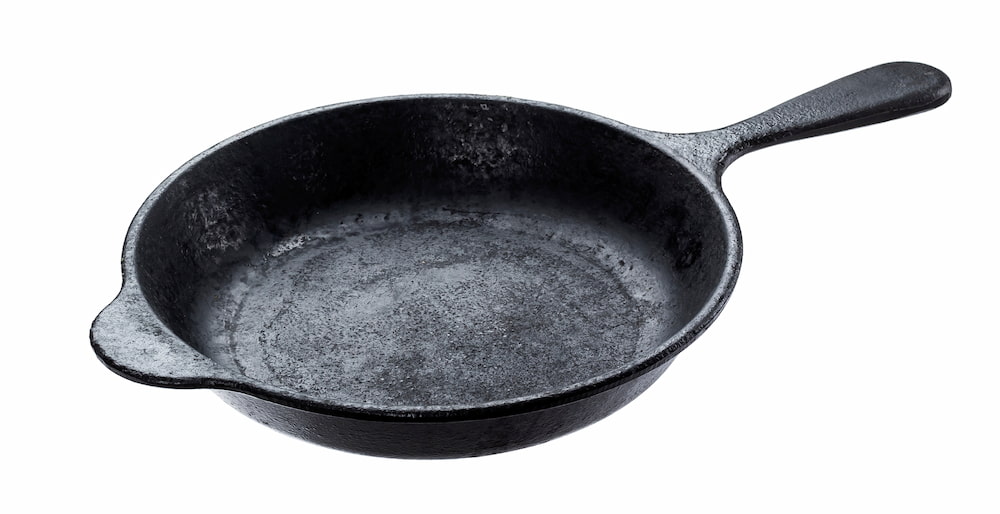
Although cast iron is brittle, its hardness makes it resistant to wear. The final form of a cast iron product is gained through casting. This process only needs minor after-treatment, making it possible to form the needed shape.
The properties of cast iron:
- Great castability
- Relatively cheap
- High compressive strength
- Good wear resistance
- Low melting point
What Is a Non-Ferrous Metal?
Non-ferrous metals do not contain iron. They are softer and therefore more malleable. They have industrial uses as well as aesthetic purposes – precious metals like gold and silver are both non-ferrous. Actually, all pure metal forms, except for pure iron, are non-ferrous.
Non-Ferrous Metals’ Properties
Non-ferrous metals’ advantages make them usable in many applications instead or iron and steel.
The properties of non-ferrous metals:
- High corrosion resistance
- Easy to fabricate – machinability, casting, welding, etc
- Great thermal conductivity
- Great electrical conductivity
- Low density (less mass)
- Colourful
- Non-magnetic
Non-Ferrous Metals List
Again, we are going to provide some information on each metal and its properties. Some examples of non-ferrous metals:
Copper
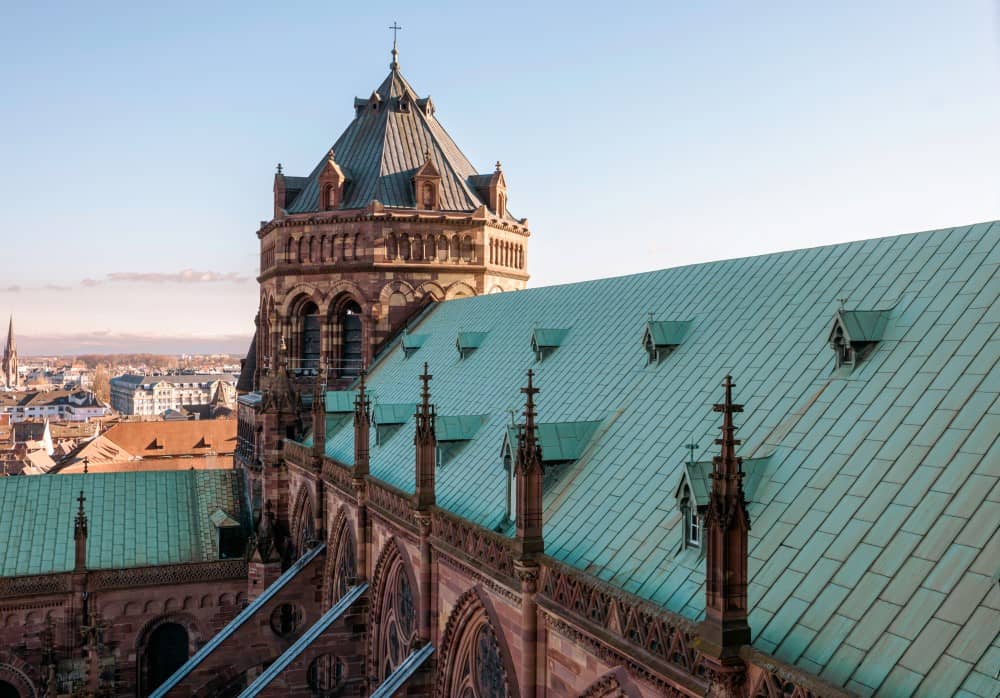
Copper is pretty widely spread in the industrial sphere. Add the alloys brass (copper and zinc) and bronze (copper and tin), and you may already see the many uses of copper. If not, we can help you out. For mechanical engineers, slide bearings and bushings may be the most known uses.
Still, copper and copper alloy properties allow more applications:
- High thermal conductivity – heat exchangers, heating vessels and appliances, etc
- High electrical conductivity – used as an electrical conductor in wiring and motors
- Good corrosion resistance – beautiful but expensive roofing
- High ductility – makes the material very easily formable and suitable for making statues
Aluminium
In engineering terms, it is a very special and important metal. It may not be so useful in everyday applications because of the price, but its combination of low weight and great machinability makes it the go-to metal in yachts, planes and many automotive parts.
Aluminium is also the base metal in many alloys. The best-known aluminium grades are probably duralumin, Y-alloy and magnalium.
Aluminium properties include:
- Corrosion resistant
- Good conductor of heat and electricity (but less than copper) – in combination with ductility and malleability, replaces copper in some instances
- High ductility and lightweight
- Becomes hard after cold working, so needs annealing
Aluminium laser cutting is something that needs expertise and the right machinery. So, choose your subcontractor for manufacturing carefully.
Lead
For the average person, lead may ring a bell related to bullets (which are now without lead) and gas (which has the sign “unleaded”). Although at first added to fuel to decrease motor knocks, it turned out to be heavily unhealthy when vaporised into the atmosphere.
The same goes for bullets and shooting range employees who have developed health problems because of it. But why add it in the first place? Because lead is the heaviest common metal. As it doesn’t react easily with other substances, they are still used in batteries and power cables, acid tanks and water pipes.
Lead properties are:
- Very heavy
- Resistant to corrosion – doesn’t react with many chemicals
- Soft and malleable
Zinc
Zinc on its own doesn’t mean much to the average person. On the other hand, as an alloying element, zinc has a wide range of purposes. It is mainly used for galvanising steel in all kinds of industries and sectors. Galvanising makes materials more durable against corrosion.
Ferrous or non-ferrous, Fractory can take care of your sheet metal fabrication and CNC machining jobs. from prototyping to large-scale manufacturing.